Sliding bearing rigidity recognition method based on mill vibration mode parameters
A sliding bearing and vibration mode technology, which is applied in the field of system parameter identification, can solve the problem of large influence on the calculation results of the mode, and achieve the effect of improving model accuracy and calculation efficiency
- Summary
- Abstract
- Description
- Claims
- Application Information
AI Technical Summary
Problems solved by technology
Method used
Image
Examples
Embodiment Construction
[0025] The present invention utilizes a Φ7.32×12.5m ball mill. The parts include foundation, fixed-end sliding bearing, free-end sliding bearing, cylinder, and large gear. The finite element components include 86164 3D units and 15603 2D Units, 660 rod units and 3805 point units; the specific steps are as follows:
[0026] 1) Establish the overall finite element model of the mill and perform modal calculations; in the finite element software of MSC.PATRAN&MSC.NASTRAN, the oil film is simplified into multiple rows of equivalent spring units, which have radial and tangential directions under the corresponding cylindrical coordinates. , Stiffness values in three axial directions;
[0027] 2) Design the test plan; use the PCB low-frequency three-way sensor to measure the vibration signal of the mill, input the signal to the OROS data acquisition instrument, and finally transmit it to the computer and record it; the determination of the position of the measuring point and the dir...
PUM
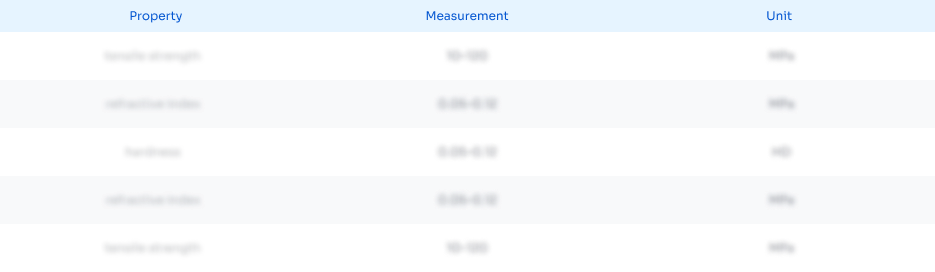
Abstract
Description
Claims
Application Information

- R&D
- Intellectual Property
- Life Sciences
- Materials
- Tech Scout
- Unparalleled Data Quality
- Higher Quality Content
- 60% Fewer Hallucinations
Browse by: Latest US Patents, China's latest patents, Technical Efficacy Thesaurus, Application Domain, Technology Topic, Popular Technical Reports.
© 2025 PatSnap. All rights reserved.Legal|Privacy policy|Modern Slavery Act Transparency Statement|Sitemap|About US| Contact US: help@patsnap.com