Method for producing basic chromic sulfate by utilizing tannery waste chromium mud
A technology of chromium sulfate and chromium mud, applied in the directions of chromium sulfate, chromium trioxide, chromium oxide/hydrate, etc., can solve the problems of environmental pollution, waste of energy, etc., and achieves the solution of chromium pollution, easy content control, significant economic benefits and high efficiency. The effect of social benefit
- Summary
- Abstract
- Description
- Claims
- Application Information
AI Technical Summary
Problems solved by technology
Method used
Examples
Embodiment 1
[0032] The present invention utilizes tannery waste chrome mud to produce the method for basic chromium sulfate, and the detailed steps of this production method are as follows:
[0033] a, at first the tanning waste chromium mud is carried out cool and dry, the mass percentage composition of water in the chrome mud after cool and sun is 36%; Then carry out drying (the waste heat that adopts roasting process to produce is dried), the gained chromium after drying The mass percent composition of water in the mud is 8%;
[0034] B, the chromium mud after step a drying is mixed with sodium hydroxide (the mass percentage composition of sodium hydroxide is 80%), and the weight ratio between chrome mud and sodium hydroxide is 1:33, Put into batch type rotary kiln after mixing, and add oxidant sodium nitrate (sodium nitrate is an industrial product, its mass percentage content is 98%), the addition of sodium nitrate accounts for 4% of the chromium mud weight after drying, then heat ;...
Embodiment 2
[0039] The present invention utilizes tannery waste chrome mud to produce the method for basic chromium sulfate, and the detailed steps of this production method are as follows:
[0040] a, at first carry out cool drying to tanning waste chrome mud, the mass percentage composition of water in the chrome mud after cooling is 30%; Then carry out drying (the waste heat that adopts roasting process to produce is dried), the gained chromium after drying The mass percent composition of water in the mud is 5%;
[0041] B, the chromium mud after step a drying is mixed with sodium hydroxide (the mass percentage composition of sodium hydroxide is 60%), and the weight ratio between chrome mud and sodium hydroxide is 1:35, Put into batch type rotary kiln after mixing, and add oxidant sodium nitrate (sodium nitrate is an industrial product, its mass percentage content is 98%), the addition of sodium nitrate accounts for 3% of the chrome mud weight after drying, then heat ; First, heat up ...
Embodiment 3
[0046] The present invention utilizes tannery waste chrome mud to produce the method for basic chromium sulfate, and the detailed steps of this production method are as follows:
[0047] a, at first carry out cool drying to tanning waste chrome mud, the mass percentage composition of water in the chrome mud after cooling is 40%; Then carry out drying (the waste heat that adopts roasting process to produce is dried), the gained chromium after drying The mass percent composition of water in the mud is 10%;
[0048] B, the chromium mud after step a drying is mixed with sodium hydroxide (the mass percentage composition of sodium hydroxide is 98%), and the weight ratio between chrome mud and sodium hydroxide is 1:30, Put into batch type rotary kiln after mixing, and add oxidant sodium nitrate (sodium nitrate is an industrial product, its mass percentage content is 98%), the addition of sodium nitrate accounts for 5% of the chromium mud weight after drying, then heat ;Firstly, heat...
PUM
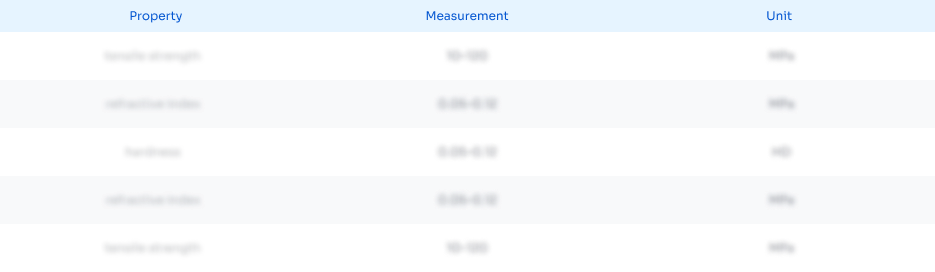
Abstract
Description
Claims
Application Information

- Generate Ideas
- Intellectual Property
- Life Sciences
- Materials
- Tech Scout
- Unparalleled Data Quality
- Higher Quality Content
- 60% Fewer Hallucinations
Browse by: Latest US Patents, China's latest patents, Technical Efficacy Thesaurus, Application Domain, Technology Topic, Popular Technical Reports.
© 2025 PatSnap. All rights reserved.Legal|Privacy policy|Modern Slavery Act Transparency Statement|Sitemap|About US| Contact US: help@patsnap.com