Exhaust pipe based laser welding plate gap control method
A technology of laser welding and control method, applied in laser welding equipment, welding equipment, manufacturing tools, etc., to achieve the effect of not affecting the forming quality and avoiding the surface quality problem of the plate
- Summary
- Abstract
- Description
- Claims
- Application Information
AI Technical Summary
Problems solved by technology
Method used
Examples
Embodiment
[0016] The present invention is a method for controlling the clearance of a laser-welded plate based on an exhaust pipe. The thickness opening of the material opening is set at intervals. The thickness opening is open on the thinner side of the material. The area of the binder surface is correspondingly larger, and the corresponding part of the die and punch is correspondingly smaller. Using the punch makes the laser melting During the welding process, there is a gap between the clamped outer plate and the inner plate in the overlapping area. The mold structure is used to form the weld part first to control the movement of the weld, and a reasonable reinforcing rib is designed near the weld. The mold structure first shapes the weld area to control the movement of the weld. The punch is formed by stamping again on the stamped inner plate with a punch and a die. The welds are straight lines. The punch is on the outer surface of the inner plate. In this embodiment, a punch i...
PUM
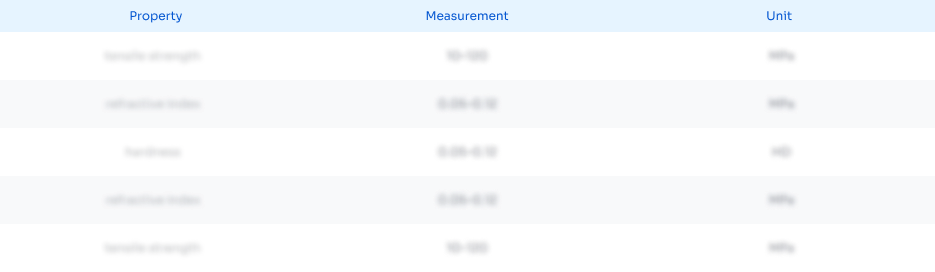
Abstract
Description
Claims
Application Information

- R&D Engineer
- R&D Manager
- IP Professional
- Industry Leading Data Capabilities
- Powerful AI technology
- Patent DNA Extraction
Browse by: Latest US Patents, China's latest patents, Technical Efficacy Thesaurus, Application Domain, Technology Topic, Popular Technical Reports.
© 2024 PatSnap. All rights reserved.Legal|Privacy policy|Modern Slavery Act Transparency Statement|Sitemap|About US| Contact US: help@patsnap.com