Magnetic resistance type electromagnetic active vibration absorber
A shock absorber and reluctance type technology, applied in the direction of shock absorber, magnetic spring, spring/shock absorber, etc., can solve the problems of nonlinearity, volume and mass reduction, etc., and achieve strong engineering applicability and convenient disassembly and assembly , good anti-swing and impact resistance
- Summary
- Abstract
- Description
- Claims
- Application Information
AI Technical Summary
Problems solved by technology
Method used
Image
Examples
Embodiment Construction
[0027] Referring to the accompanying drawings, a reluctance type electromagnetic active vibration absorber includes: a housing composed of a lower mounting plate 1 of the vibration absorber, a cover 2 of the vibration absorber and an upper mounting plate 3 of the vibration absorber, and a mover assembly located inside the housing and stator assembly;
[0028] The mover assembly includes: two mover silicon steel sheets 12 with permanent magnets 11 embedded in the central groove of the end face; the two mover silicon steel sheets 12 are placed parallel to each other on the lower mounting plate 1 of the vibration absorber, and are installed with the lower vibration absorber. The plate 1 is vertical, and the end embedded with the permanent magnet 11 is opposite to each other. The two sides of each mover silicon steel sheet 12 respectively pass through the mover fixing screw 10 and the left fixed plate 6 of the mover silicon steel sheet, and the right fixed plate of the mover silico...
PUM
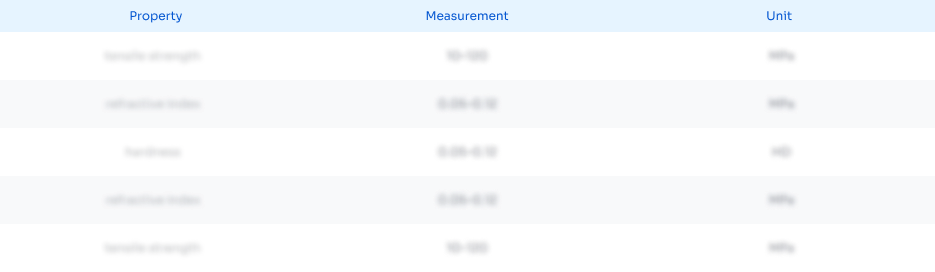
Abstract
Description
Claims
Application Information

- R&D
- Intellectual Property
- Life Sciences
- Materials
- Tech Scout
- Unparalleled Data Quality
- Higher Quality Content
- 60% Fewer Hallucinations
Browse by: Latest US Patents, China's latest patents, Technical Efficacy Thesaurus, Application Domain, Technology Topic, Popular Technical Reports.
© 2025 PatSnap. All rights reserved.Legal|Privacy policy|Modern Slavery Act Transparency Statement|Sitemap|About US| Contact US: help@patsnap.com