Emulsion breaker for thick oil and preparation method and application of emulsion breaker
A demulsifier and heavy oil technology, which is applied in the field of demulsifier for heavy oil and its preparation, can solve the problems of slow crude oil dehydration process, poor demulsifier effect, and large product dosage, and achieves good demulsification effect, easy control, and production. low cost effect
- Summary
- Abstract
- Description
- Claims
- Application Information
AI Technical Summary
Problems solved by technology
Method used
Image
Examples
Embodiment 1
[0022] In the embodiment of the present invention, a demulsifier for heavy oil is composed of the following raw materials in parts by weight: 1 part of cocoyl diethanolamine, 7 parts of maleic acid, 25 parts of zeolite, and 5 parts of polyglycerol fatty acid ester .
[0023] Maleic acid is mixed with deionized water with 4 times of its quality to make maleic acid solution; Cocoyl diethanolamine is mixed with 40% ethanol at a volume concentration of 5 times its quality to make cocoyl diethanolamine Diethanolamine solution. Grind the zeolite, pass through a 120-mesh sieve, add maleic acid solution, and stir at 80°C for 20 minutes, then raise the temperature to 125°C and heat and stir for 10 minutes to prepare mixture A. Mix polyglycerol fatty acid ester and cocoamide diethanolamine solution, heat and stir at 55° C. for 30 minutes, and prepare mixture B. Mix mixture A and mixture B, heat and stir at 165°C for 50 minutes, and then calcinate at 450°C for 4 hours to obtain a demul...
Embodiment 2
[0025] In the embodiment of the present invention, a demulsifier for heavy oil is composed of the following raw materials in parts by weight: 5 parts of cocoyl diethanolamine, 15 parts of maleic acid, 35 parts of zeolite, and 12 parts of polyglycerol fatty acid ester .
[0026] Maleic acid is mixed with deionized water with 4 times its mass to prepare a maleic acid solution; cocoamide diethanolamine is mixed with 40% ethanol with 5 times its mass to obtain a cocoamide diethanolamine solution. Grind the zeolite, pass through a 120-mesh sieve, add maleic acid solution, and stir at 80°C for 20 minutes, then raise the temperature to 125°C and heat and stir for 10 minutes to prepare mixture A. Mix polyglycerol fatty acid ester and cocoamide diethanolamine solution, and heat and stir at 55°C for 40 minutes to prepare mixture B. Mix mixture A and mixture B, heat and stir at 165°C for 60 minutes, and then calcinate at 450°C for 4 hours to obtain a demulsifier.
Embodiment 3
[0028] In the embodiment of the present invention, a demulsifier for heavy oil is composed of the following raw materials in parts by weight: 2 parts of cocoyl diethanolamine, 9 parts of maleic acid, 28 parts of zeolite, and 7 parts of polyglycerol fatty acid ester .
[0029] Maleic acid is mixed with deionized water with 4 times its mass to prepare a maleic acid solution; cocoamide diethanolamine is mixed with 40% ethanol with 5 times its mass to obtain a cocoamide diethanolamine solution. Grind the zeolite, pass through a 120-mesh sieve, add maleic acid solution, and stir at 80°C for 20 minutes, then raise the temperature to 125°C and heat and stir for 10 minutes to prepare mixture A. Mix polyglycerol fatty acid ester and cocoamide diethanolamine solution, and heat and stir at 55°C for 35 minutes to prepare mixture B. Mix mixture A and mixture B, heat and stir at 165°C for 55 minutes, and then calcinate at 450°C for 4 hours to obtain a demulsifier.
PUM
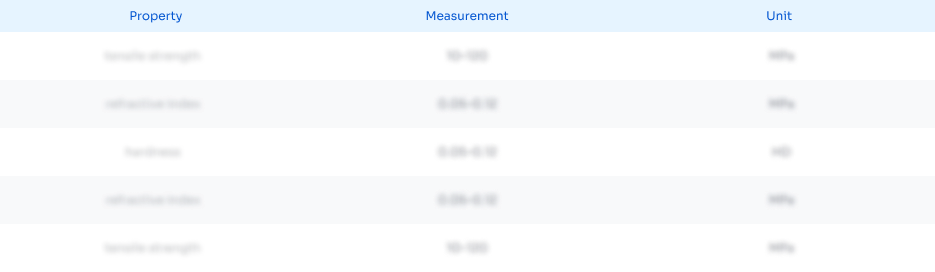
Abstract
Description
Claims
Application Information

- R&D Engineer
- R&D Manager
- IP Professional
- Industry Leading Data Capabilities
- Powerful AI technology
- Patent DNA Extraction
Browse by: Latest US Patents, China's latest patents, Technical Efficacy Thesaurus, Application Domain, Technology Topic, Popular Technical Reports.
© 2024 PatSnap. All rights reserved.Legal|Privacy policy|Modern Slavery Act Transparency Statement|Sitemap|About US| Contact US: help@patsnap.com