Preparation method of heat preservation and insulation high polymer material
A polymer material, thermal insulation technology, applied in the field of preparation of thermal insulation polymer materials, can solve problems such as poor heat resistance, incomplete satisfaction, casualties, etc., to overcome poor durability, reduce processing costs, and service life. long effect
- Summary
- Abstract
- Description
- Claims
- Application Information
AI Technical Summary
Problems solved by technology
Method used
Examples
preparation example Construction
[0031] A method for preparing a thermal insulation polymer material, comprising the steps of:
[0032] A, the plant biomass waste is crushed;
[0033] B. Soak the pulverized plant biomass waste with a strong alkali solution, neutralize the alkalinity, and dry to obtain activated plant biomass waste;
[0034] C. Activate plant biomass waste according to the mass ratio: functional monomer: initiator: dispersant = 1000: 10-20: 0-2: 0-100 for reaction, and after the reaction, the surface grafted modified plant biomass can be obtained. material waste powder;
[0035] D. According to the mass ratio surface grafting modified plant biomass waste powder: flow modified monomer: initiator: dispersant = 1000: 10~20: 1~2: 1~10 for mixing and granulation to obtain improved Post-destructive plant biomass waste dry powder;
[0036] E. Plant biomass waste dry powder modified according to the mass ratio: polyvinyl chloride: processing aid: filler = 700-1000: 0-300: 10-30: 0-20 mixed and gran...
Embodiment 1
[0047] A: The wheat straw is recycled, and then the wheat straw is crushed so that the grain size of the wheat straw reaches 80 mesh.
[0048] B: Weigh 1000 g of 80-mesh wheat straw, place it in a reaction kettle, add 6 L of inorganic strong alkali sodium hydroxide solution, and soak for 24 hours. After soaking for 24 hours, the sodium hydroxide was filtered out, and purified water was added to clean the wheat straw powder. Add pure water several times to clean until the pH value of the cleaning solution is about 7. Then carry out drying treatment, and the activated wheat straw can be obtained only when the water content reaches below 0.1%.
[0049] C: At room temperature, mix 1000g of activated wheat straw, 20g of succinic anhydride, 2g of glutaric acid peroxide, and 1g of polyvinyl alcohol, and then put the mixed material into a hot mixer for thermal surface modification. The temperature was controlled at 120° C., and the rotational speed of the mixer was at 8 rpm to obtai...
Embodiment 2
[0061] A: The bagasse is recovered, and then the bagasse is crushed to make the bagasse particle size reach 60 mesh.
[0062] B: Weigh again 1000g of 60-mesh bagasse, place it in a reaction kettle, add 6L of inorganic strong alkali sodium hydroxide solution, and soak for 24 hours. After soaking for 24 hours, the sodium hydroxide was filtered out, and purified water was added to clean the bagasse powder. Adding pure water several times to wash until the pH value of the cleaning solution is about 7, and then performing drying treatment, and the activated bagasse can be obtained when the water content reaches below 0.1%.
[0063] C: Mix 1000g of activated bagasse and 10g of hexanoic anhydride, put the mixed material into a hot mixer for thermal surface modification, control the temperature at 100°C, and the speed of the mixer at 30rpm to obtain a surface contact surface. Modified bagasse powder.
[0064] D: Mix 1000g surface-grafted modified bagasse powder, 10g methyl acrylate,...
PUM
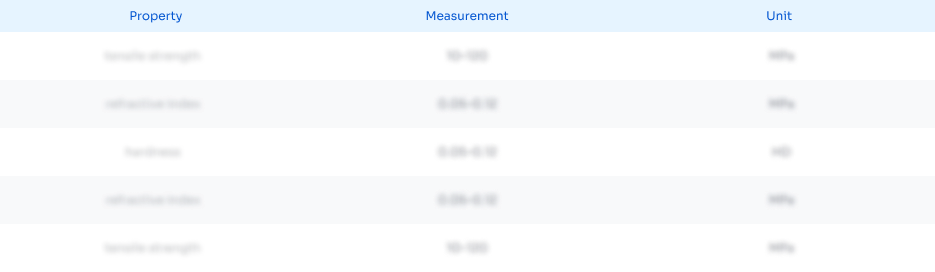
Abstract
Description
Claims
Application Information

- Generate Ideas
- Intellectual Property
- Life Sciences
- Materials
- Tech Scout
- Unparalleled Data Quality
- Higher Quality Content
- 60% Fewer Hallucinations
Browse by: Latest US Patents, China's latest patents, Technical Efficacy Thesaurus, Application Domain, Technology Topic, Popular Technical Reports.
© 2025 PatSnap. All rights reserved.Legal|Privacy policy|Modern Slavery Act Transparency Statement|Sitemap|About US| Contact US: help@patsnap.com