Cowhells color rubber composition for tire tread of load bearing radial tire
A rubber composition and technology for radial tires, applied in the direction of rolling resistance optimization, road transportation emission reduction, etc., to achieve the effects of promoting development, increasing aesthetics, and reducing rolling resistance
- Summary
- Abstract
- Description
- Claims
- Application Information
AI Technical Summary
Problems solved by technology
Method used
Image
Examples
Embodiment 1
[0017] In this example, each component of the composition is measured in parts by mass, and the specific components are shown in Table 1. The kneading of the rubber composition can be carried out by methods known to those skilled in rubber kneading. For example, each component is generally mixed in at least two stages. The mixing process of the rubber composition is to use a closed rubber mixer to masticate the natural rubber for 3 to 4 minutes, and the temperature is discharged within the range of 155 to 165 ° C. After the film is parked for 8 hours, add a section of plasticized rubber, synthetic rubber, highly dispersible white carbon black and all compounding agents except the vulcanization system to the closed rubber mixer, and mix 3~4 minutes, discharge the rubber in the range of 150~160℃, and complete the preparation of the second-stage master batch; after the film is parked for 8 hours, add the second-stage master batch and all the compounding agents of the vulcanizatio...
Embodiment 2
[0023] The difference from Example 1 is that the raw materials in parts by mass as shown in Table 2 are selected.
[0024] The kneading of the rubber composition can be carried out by methods known to those skilled in rubber kneading. The mixing process of the rubber composition is to use a closed rubber mixer to masticate the natural rubber for 3 to 4 minutes, and discharge the rubber at a temperature of 155 to 165°C to complete the preparation of a section of masticated rubber; after the film is parked for 8 hours, Then add plasticized rubber, synthetic rubber, highly dispersible white carbon black and all compounding agents except the vulcanization system to the closed rubber mixer, and mix for 3-4 minutes to discharge the glue in the range of 150-160°C to complete the second stage Preparation of masterbatch: After the film is parked for 8 hours, add the second-stage masterbatch and all the compounding ingredients of the vulcanization system into the closed rubber mixer, an...
Embodiment 3
[0030] The difference from Examples 1 and 2 is that the raw materials in parts by mass as shown in Table 3 are selected.
[0031] The kneading of the rubber composition can be carried out by methods known to those skilled in rubber kneading. The mixing process of the rubber composition is to use a closed rubber mixer to masticate the natural rubber for 3 to 4 minutes, and discharge the rubber at a temperature of 155 to 165°C to complete the preparation of a section of masticated rubber; after the film is parked for 8 hours, Then add plasticized rubber, synthetic rubber, highly dispersible white carbon black and all compounding agents except the vulcanization system to the closed rubber mixer, and mix for 3-4 minutes to discharge the glue in the range of 150-160°C to complete the second stage Preparation of masterbatch: After the film is parked for 8 hours, add the second-stage masterbatch and all the compounding ingredients of the vulcanization system into the closed rubber mi...
PUM
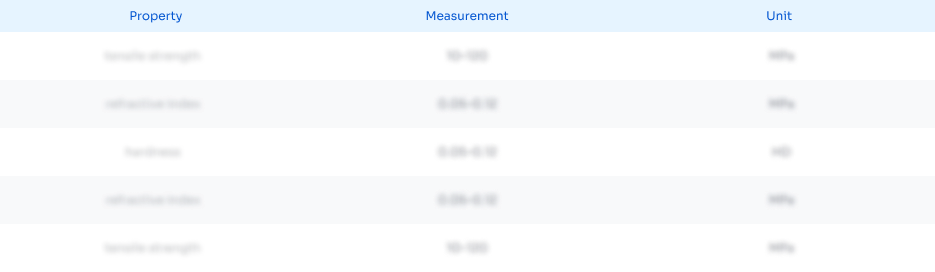
Abstract
Description
Claims
Application Information

- R&D
- Intellectual Property
- Life Sciences
- Materials
- Tech Scout
- Unparalleled Data Quality
- Higher Quality Content
- 60% Fewer Hallucinations
Browse by: Latest US Patents, China's latest patents, Technical Efficacy Thesaurus, Application Domain, Technology Topic, Popular Technical Reports.
© 2025 PatSnap. All rights reserved.Legal|Privacy policy|Modern Slavery Act Transparency Statement|Sitemap|About US| Contact US: help@patsnap.com