Production process of RFID tag ultrahigh frequency antenna
A technology of RFID tags and production processes, which is applied in the directions of tags, antennas, and antenna parts to achieve the effects of easy decomposition, increased selectivity, and environmental protection.
- Summary
- Abstract
- Description
- Claims
- Application Information
AI Technical Summary
Problems solved by technology
Method used
Examples
Embodiment 1
[0021] A kind of production technology of RFID label ultra-high frequency antenna, it comprises the following steps:
[0022] Step 1: First prepare the required composite glue, and then use the composite machine to coat the glue on the coated paper and then composite it with aluminum foil to produce a composite film. The glue is cured through the oven of the composite machine to complete the composite process. The middle composite glue is made by mixing two-component high-temperature cooking adhesive, curing agent and ethyl ester. The two-component high-temperature cooking adhesive adopts 430 glue, and the curing agent adopts 105N curing agent, and the specific ratio is, two-component type High temperature cooking adhesive: curing agent: ethyl ester = 6:2:10. The composite parameters are: the speed of the composite roller is 40m / min, the pressure of the glue roller is 0.5Mpa, the tension of the scraper is 0.6Mpa, the tension of the pendulum is 0.1N, the air pressure of the com...
Embodiment 2
[0027] A kind of production technology of RFID label ultra-high frequency antenna, it comprises the following steps:
[0028] Step 1: First prepare the required composite glue, and then use the composite machine to coat the glue on the coated paper and then composite it with aluminum foil to produce a composite film. The glue is cured through the oven of the composite machine to complete the composite process. The middle composite glue is made by mixing two-component high-temperature cooking adhesive, curing agent and ethyl ester. The two-component high-temperature cooking adhesive adopts 430 glue, and the curing agent adopts 105N curing agent, and the specific ratio is, two-component type High temperature cooking adhesive: curing agent: ethyl ester = 6:2:10. The composite parameters are: the speed of the composite roller is 50m / min, the pressure of the glue roller is 0.8Mpa, the tension of the scraper is 1Mpa, the tension of the pendulum is 0.3N, the air pressure of the compo...
PUM
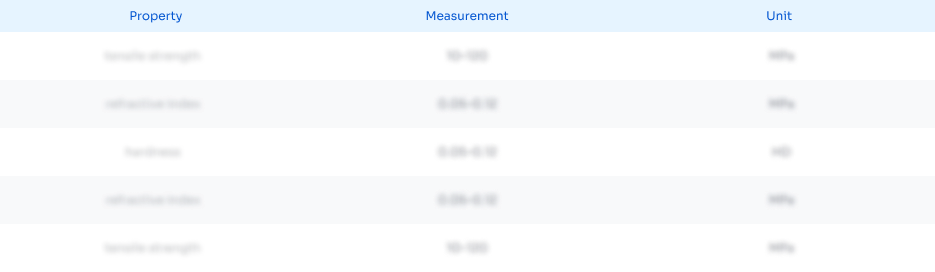
Abstract
Description
Claims
Application Information

- Generate Ideas
- Intellectual Property
- Life Sciences
- Materials
- Tech Scout
- Unparalleled Data Quality
- Higher Quality Content
- 60% Fewer Hallucinations
Browse by: Latest US Patents, China's latest patents, Technical Efficacy Thesaurus, Application Domain, Technology Topic, Popular Technical Reports.
© 2025 PatSnap. All rights reserved.Legal|Privacy policy|Modern Slavery Act Transparency Statement|Sitemap|About US| Contact US: help@patsnap.com