Resin self-hardening core sand for casting train iron castings and preparing method of resin self-hardening core sand
A technology for casting resin and iron castings. It is applied to casting molding equipment, casting molds, and cores. It can solve the problems of surface micro-cracks, easy expansion when heated, and large gas generation, and achieves improved sand sticking, good collapsibility, and The effect of reducing the generation of gas
- Summary
- Abstract
- Description
- Claims
- Application Information
AI Technical Summary
Problems solved by technology
Method used
Image
Examples
Embodiment 1
[0016] A resin self-hardening core sand for train iron castings, which is prepared from the following raw materials in parts by weight (kg): sea sand 160, corundum 20, dead-burned magnesia 16, paper clay 10, chalk 6, furan resin 10 , cashew nut shell oil modified phenolic resin 12, polyimide 4, rare earth tailings 3, white boronite 5, waste foam glass 8, ferrosilicon nitride 3, N-(β-aminoethyl)-γ- Aminopropyltriethoxysilane 1, p-toluenesulfonic acid 2, phosphoric acid 3, castor oil maleic anhydride 4, triphenylmethane triisocyanate 8, styrene 2.
[0017] A method for preparing resin self-hardening core sand for railway iron castings, comprising the following steps:
[0018] (1) Mix rare earth tailings, white boronite, and waste foam glass evenly, break them into 80-90 mesh, and then pour them into the sand mixer together with sea sand, corundum, dead-burned magnesia, paper clay, and chalk Mix for 3-5 minutes, then dry at 120-130°C for 3-5 hours until the water content is belo...
Embodiment 2
[0022] A resin no-hardening core sand for train iron castings, which is prepared from the following raw materials in parts by weight (kg): sea sand 170, corundum 25, dead-burned magnesia 18, paper clay 12, chalk 7, furan resin 12.5 , cashew nut shell oil modified phenolic resin 13, polyimide 5, rare earth tailings 4, white boronite 6, waste foam glass 9, ferrosilicon nitride 4, N-(β-aminoethyl)-γ- Aminopropyltriethoxysilane 1.5, p-toluenesulfonic acid 3, phosphoric acid 4, castor oil maleic anhydride 5, triphenylmethane triisocyanate 9, styrene 3.
[0023] The preparation method is the same as in Example 1.
Embodiment 3
[0025] A resin no-hardening core sand for train iron castings, which is prepared from the following raw materials in parts by weight (kg): sea sand 180, corundum 30, dead-burned magnesia 20, paper clay 14, chalk 8, furan resin 15 , cashew nut shell oil modified phenolic resin 14, polyimide 6, rare earth tailings 5, white boronite 7, waste foam glass 10, ferrosilicon nitride 5, N-(β-aminoethyl)-γ- Aminopropyltriethoxysilane 2, p-toluenesulfonic acid 4, phosphoric acid 5, castor oil maleic anhydride 6, triphenylmethane triisocyanate 10, styrene 4.
[0026] The preparation method is the same as in Example 1.
[0027] The performance testing result of the resin self-hardening core sand that above-mentioned embodiment 1-3 makes is shown in the table below:
[0028]
PUM
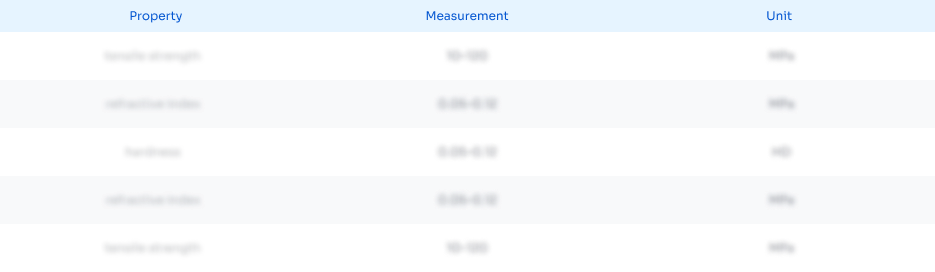
Abstract
Description
Claims
Application Information

- R&D Engineer
- R&D Manager
- IP Professional
- Industry Leading Data Capabilities
- Powerful AI technology
- Patent DNA Extraction
Browse by: Latest US Patents, China's latest patents, Technical Efficacy Thesaurus, Application Domain, Technology Topic, Popular Technical Reports.
© 2024 PatSnap. All rights reserved.Legal|Privacy policy|Modern Slavery Act Transparency Statement|Sitemap|About US| Contact US: help@patsnap.com