Surface modification method for diamond micropowder for ultra-fine diamond wire saw
A technology of diamond micropowder and diamond wire saw, which is applied in the direction of coating, electrolytic coating, etc., can solve the problems of poor dispersion performance, uneven wire diameter, poor activation effect, etc., achieve fast plating adhesion and improve hydrophilicity , the effect of preventing pollution
- Summary
- Abstract
- Description
- Claims
- Application Information
AI Technical Summary
Problems solved by technology
Method used
Examples
Embodiment 1
[0022] The method for modifying the surface of diamond micropowder for ultra-fine diamond wire saw comprises the following steps:
[0023] (1) Calcining the diamond micropowder after electroless plating at 200°C for 2 hours;
[0024] (2) The calcined diamond powder is acid-washed and activated with a compound acid whose mass concentration is respectively 1% of sulfuric acid and citric acid, and the drum is stirred for 3 minutes, and deacidified by filtration after activation;
[0025] (3) Alkane sulfonate cationic surfactant and deionized water are mixed according to the mass ratio of 1:1000, then add the diamond micropowder after deacidification and stir, and disperse;
[0026] (4) After dispersing, add the diamond micropowder together with the cationic surfactant into the electroplating solution, stir and disperse evenly, and set aside.
Embodiment 2
[0028] The method for modifying the surface of diamond micropowder for ultra-fine diamond wire saw comprises the following steps:
[0029] (1) Calcining the diamond micropowder after electroless plating for 1.5 hours at 250°C;
[0030] (2) The calcined diamond powder is acid-washed and activated with a compound acid whose mass concentration is respectively 5% sulfuric acid and citric acid, and the drum is stirred for 5 minutes, and deacidified by filtration after activation;
[0031] (3) Alkane sulfonate cationic surfactant and deionized water are mixed according to the mass ratio of 5:1000, then add the diamond micropowder after deacidification and stir, and disperse;
[0032] (4) After dispersing, add the diamond micropowder together with the cationic surfactant into the electroplating solution, stir and disperse evenly, and set aside.
Embodiment 3
[0034] The method for modifying the surface of diamond micropowder for ultra-fine diamond wire saw comprises the following steps:
[0035] (1) Calcining the diamond micropowder after electroless plating at 300° C. for 1 hour;
[0036] (2) The calcined diamond micropowder is acid-washed and activated with a compound acid whose mass concentration is respectively 3% sulfuric acid and citric acid, and the drum is stirred for 4 minutes, and deacidified by filtration after activation;
[0037] (3) Alkane sulfonate cationic surfactant and deionized water are mixed according to the mass ratio of 2:1000, then add the diamond micropowder after deacidification and stir, and disperse;
[0038] (4) After dispersing, add the diamond micropowder together with the cationic surfactant into the electroplating solution, stir and disperse evenly, and set aside.
PUM
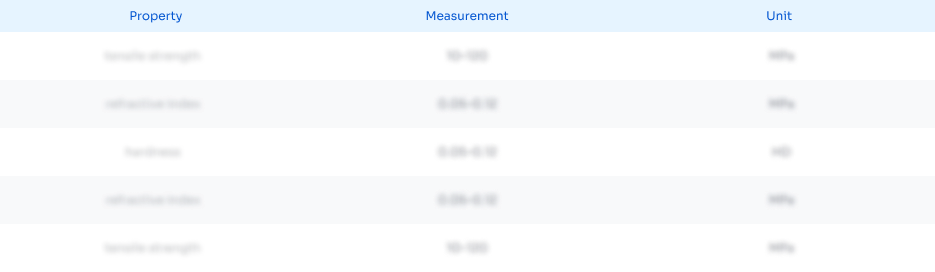
Abstract
Description
Claims
Application Information

- R&D
- Intellectual Property
- Life Sciences
- Materials
- Tech Scout
- Unparalleled Data Quality
- Higher Quality Content
- 60% Fewer Hallucinations
Browse by: Latest US Patents, China's latest patents, Technical Efficacy Thesaurus, Application Domain, Technology Topic, Popular Technical Reports.
© 2025 PatSnap. All rights reserved.Legal|Privacy policy|Modern Slavery Act Transparency Statement|Sitemap|About US| Contact US: help@patsnap.com