Integrated injection molding rotor and stepping motor applied to automatic control
An integrated, injection molding technology, applied in the control of mechanical energy, electrical components, electromechanical devices, etc., can solve the problem of the deterioration of the rotor outer diameter and the coaxiality of the rotor shaft, the higher requirements for operators and the environment, and the lack of positioning accuracy. Control requirements and other issues, to achieve the effect of small coaxiality error, improve motor efficiency, and reduce product noise
- Summary
- Abstract
- Description
- Claims
- Application Information
AI Technical Summary
Problems solved by technology
Method used
Image
Examples
Embodiment Construction
[0040] In order to make the content of the present invention more clearly understood, the present invention will be further described in detail below based on specific embodiments and in conjunction with the accompanying drawings.
[0041] Such as Figure 1~5 As shown, a one-piece injection molded rotor, which includes:
[0042] magnetic ring 1;
[0043] rotary axis 2;
[0044] Injection molded body 3, said injection molded body 3 is arranged between magnetic ring 1 and rotary shaft 2, so that said injection molded body 3 makes rotary shaft 2 and magnetic ring 1 into one, and said magnetic ring 1 and injection molded body 3 There is a magnetic ring limiting mechanism that locks the relative position between the magnetic ring 1 and the injection molding body 3 so as to increase the bonding fastness between the magnetic ring 1 and the injection molding body 3; this embodiment introduces a magnetic ring limiting mechanism The specific structure is as follows:
[0045] The mag...
PUM
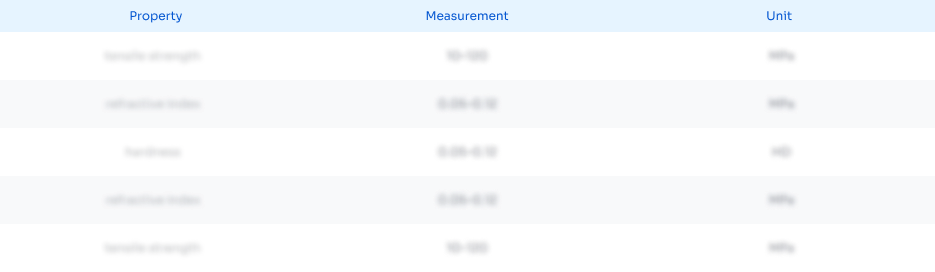
Abstract
Description
Claims
Application Information

- Generate Ideas
- Intellectual Property
- Life Sciences
- Materials
- Tech Scout
- Unparalleled Data Quality
- Higher Quality Content
- 60% Fewer Hallucinations
Browse by: Latest US Patents, China's latest patents, Technical Efficacy Thesaurus, Application Domain, Technology Topic, Popular Technical Reports.
© 2025 PatSnap. All rights reserved.Legal|Privacy policy|Modern Slavery Act Transparency Statement|Sitemap|About US| Contact US: help@patsnap.com