Fireproof polyurethane floor coating
A floor paint and polyurethane technology, applied in the field of floor paint, can solve the problems of high substrate humidity and environmental humidity, low paint film compactness, small market share, etc., and achieve complete environmental protection, high brightness, The effect of avoiding harm to human health
- Summary
- Abstract
- Description
- Claims
- Application Information
AI Technical Summary
Problems solved by technology
Method used
Examples
Embodiment 1
[0011] The polyurethane fireproof floor paint of the present embodiment comprises the following components in parts by weight: 78 parts of waterborne polyurethane resin, 20 parts of melamine formaldehyde resin, 15 parts of polyvinyl acetate emulsion, 16 parts of paraffin wax emulsion, 3 parts of alkylbenzene sulfonate, 6 parts of vinyltrimethoxysilane, 11 parts of hydroxyethyl cellulose, 3 parts of dinonyl naphthalenesulfonic acid, 1 part of butyl titanate, 4 parts of citric acid, 3 parts of zinc naphthenate, 2 parts of sodium borate, 5 parts polyurethane curing agent, 10 parts polyurethane dispersant.
Embodiment 2
[0013] The polyurethane fireproof floor paint of the present embodiment comprises the following components in parts by weight: 86 parts of waterborne polyurethane resin, 24 parts of melamine formaldehyde resin, 25 parts of polyvinyl acetate emulsion, 18 parts of paraffin wax emulsion, 7 parts of alkylbenzene sulfonate, 8 parts of vinyltrimethoxysilane, 14 parts of hydroxyethyl cellulose, 7 parts of dinonyl naphthalenesulfonic acid, 4 parts of butyl titanate, 7 parts of citric acid, 7 parts of zinc naphthenate, 4 parts of sodium borate, 12 parts of polyurethane curing agent, 15 parts of polyurethane dispersant, 15 parts of polyvinyl acetate.
Embodiment 3
[0015] The polyurethane fireproof floor paint of the present embodiment comprises the following components in parts by weight: 78 parts of waterborne polyurethane resin, 20 parts of melamine formaldehyde resin, 15 parts of polyvinyl acetate emulsion, 16 parts of paraffin wax emulsion, 3 parts of alkylbenzene sulfonate, 6 parts of vinyltrimethoxysilane, 11 parts of hydroxyethyl cellulose, 3 parts of dinonyl naphthalenesulfonic acid, 1 part of butyl titanate, 4 parts of citric acid, 3 parts of zinc naphthenate, 2 parts of sodium borate, 5 parts of polyurethane curing agent, 10 parts of polyurethane dispersant, 9 parts of polyvinyl acetate, 10 parts of liquid rosin resin.
PUM
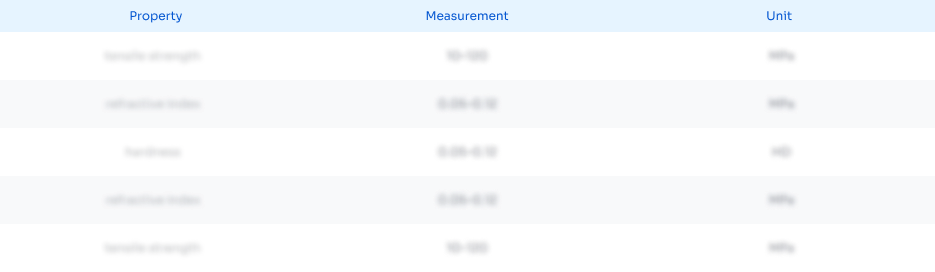
Abstract
Description
Claims
Application Information

- R&D
- Intellectual Property
- Life Sciences
- Materials
- Tech Scout
- Unparalleled Data Quality
- Higher Quality Content
- 60% Fewer Hallucinations
Browse by: Latest US Patents, China's latest patents, Technical Efficacy Thesaurus, Application Domain, Technology Topic, Popular Technical Reports.
© 2025 PatSnap. All rights reserved.Legal|Privacy policy|Modern Slavery Act Transparency Statement|Sitemap|About US| Contact US: help@patsnap.com