Pad plate for hole drilling and preparation method thereof
A backing plate and modification technology, which is applied in the field of backing plate for drilling and its preparation, can solve the problems of rising production cost of backing plate, wire entanglement of drilling needles, large warping, etc., so as to improve production efficiency and process time, the effect of reducing warpage
- Summary
- Abstract
- Description
- Claims
- Application Information
AI Technical Summary
Problems solved by technology
Method used
Examples
Embodiment 1
[0044] 1) Preparation of modified urea-formaldehyde resin
[0045] In terms of weight percentage, first add 44% formaldehyde, start stirring speed 80r / min, temperature 20°C, add 2.5% urotropine to measure pH value is 8.5, 6.5% melamine, 15% urea;
[0046] Open the steam valve, add 1 KG / C㎡ pressure to the jacket of the reaction kettle, start to heat up, and raise the temperature of the material to 70°C within 30 minutes (the reaction liquid becomes transparent at 60°C, and the pH value should be 8-8.5 at this time);
[0047] Keep warm for 30 minutes and add 14% methanol (if vacuum suction, you must open the large throttle after suction), then raise the temperature to 70°C, and keep warm for 1.5 hours. After the time is up, add 4% diethylene glycol and pass water to cool down;
[0048] Stir and cool for 40 minutes and discharge, the stirring speed is 60r / m;
[0049] Then add 10% aluminum powder to the above-mentioned released feed liquid, the stirring speed is 80r / min, and the ...
Embodiment 2
[0057] 1) Preparation of modified urea-formaldehyde resin
[0058] In terms of weight percentage, first add 42% formaldehyde, start stirring speed 90r / min, temperature 20°C, add 2% urotropine to measure pH value is 8.5, 6% melamine, 14% urea;
[0059] Open the steam valve, add 1 KG / C㎡ air pressure to the jacket of the reaction kettle, start to heat up, and raise the temperature of the material to 75°C within 30 minutes (the reaction liquid becomes transparent at 60°C, and the pH value should be 8-8.5 at this time).
[0060] Keep warm for 30 minutes and add 17% methanol (if vacuum suction, you must open the large throttle after suction), then raise the temperature to 70°C, and keep warm for 1.5 hours. After the time is up, add 5% diethylene glycol and pass water to cool down;
[0061] Stir and cool for 40 minutes and discharge, the stirring speed is 60r / m.
[0062] Then add 10% talcum powder to the feed liquid released above, the stirring speed is 80r / min, and the temperature ...
Embodiment 3
[0070] 1) Preparation of modified urea-formaldehyde resin
[0071] In terms of weight percentage, first add 46% formaldehyde, start stirring speed 90r / min, temperature 30°C, add 3% urotropine to measure pH value is 8.5, 7% melamine, 14% urea;
[0072] Open the steam valve, add 1 KG / C㎡ pressure to the jacket of the reaction kettle, start to heat up, and raise the temperature of the material to 73°C within 30 minutes (the reaction liquid becomes transparent at 60°C, and the pH value should be 8-8.5 at this time).
[0073] Keep warm for 30 minutes and add 12% methanol (if vacuum suction, you must open the large throttle after suction), then raise the temperature to 70°C, and keep warm for 1.5 hours. After the time is up, add 4% diethylene glycol and pass water to cool down;
[0074] Stir and cool for 40 minutes and discharge, stirring speed 60r / m;
[0075] Then first add 10% of the total weight of aluminum powder and wood powder mixed filler to the above-mentioned discharged fee...
PUM
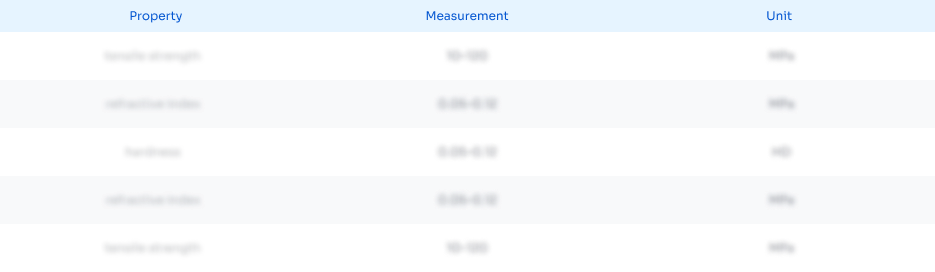
Abstract
Description
Claims
Application Information

- R&D Engineer
- R&D Manager
- IP Professional
- Industry Leading Data Capabilities
- Powerful AI technology
- Patent DNA Extraction
Browse by: Latest US Patents, China's latest patents, Technical Efficacy Thesaurus, Application Domain, Technology Topic, Popular Technical Reports.
© 2024 PatSnap. All rights reserved.Legal|Privacy policy|Modern Slavery Act Transparency Statement|Sitemap|About US| Contact US: help@patsnap.com