Continuous casting slab defect melting equipment and thermal deburring process
A continuous casting slab and burr technology, which is applied in the field of continuous casting slab defect melting equipment and thermal burr removal technology, can solve problems such as harsh working environment, high dust, high temperature, etc., to improve operating efficiency, eliminate quality problems, and save energy. artificial effect
- Summary
- Abstract
- Description
- Claims
- Application Information
AI Technical Summary
Problems solved by technology
Method used
Image
Examples
Embodiment 1
[0051] This embodiment provides a continuous casting slab defect melting equipment, including a purging unit, see the attached figure 1 As shown, the purging unit includes a flame spray gun 1, and a deburring oxygen blowing pipe 2 is added to the side of the flame spray gun 1, and the burr oxygen blowing pipe 2 has a hole diameter of 8mm. The end of the oxygen blowing pipe 2 is connected with the nozzle 3 . The oxygen blowing pipe 2 adopts an easy-to-bend structure, which is convenient for adjusting the position of the nozzle 3 and adjusting the blowing angle for deburring. In this embodiment, it is made of high-temperature-resistant copper material. Nozzle 3 is a flat nozzle, and the height of nozzle 3 is 1mm (see image 3 ), which facilitates the formation of high-pressure airflow and increases the mechanical impact performance of the gas.
[0052] combined with figure 2 As shown, the oxygen blowing pipe is connected to the burr-blowing oxygen pipeline 4, and the burr-bl...
Embodiment 2
[0055] Referring to Example 1, the burr-blowing oxygen pipeline is connected from the splitter 14 of the equipment, and an independent solenoid valve and a gas meter are set on the burr-blowing oxygen pipeline.
Embodiment 3
[0057] Adopt the thermal state deburring process of the continuous casting slab defect melting equipment of embodiment 1 or 2, comprising,
[0058](1) Preparation, the nozzle 3 of the oxygen blowing pipe 2 is arranged behind the walking direction of the flame spray gun 1, the distance from the flame spray gun nozzle 13 is 150-200mm, and the height is positioned to 15-18mm from the surface of the slab;
[0059] (2) When the equipment is working, when the continuous casting slab defect melting device is purging the surface of the slab, at the starting point of self-purging, the solenoid valve will automatically open the oxygen blowing pipe, and set the low pressure of 0.5-0.7Mpa into the oxygen blowing pipe Oxygen, the purging unit moves at a speed of 7-9M / min;
[0060] (3) After the purge unit reaches the end point of slab purge, control the flame spray gun to turn off, and the oxygen blowing pipe continues to blow oxygen, and the purge unit returns to the starting point at a w...
PUM
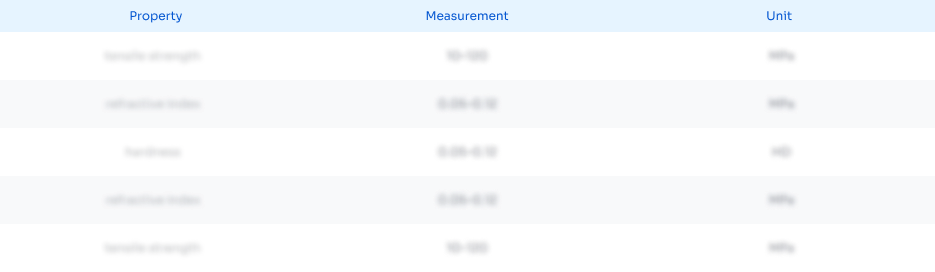
Abstract
Description
Claims
Application Information

- R&D
- Intellectual Property
- Life Sciences
- Materials
- Tech Scout
- Unparalleled Data Quality
- Higher Quality Content
- 60% Fewer Hallucinations
Browse by: Latest US Patents, China's latest patents, Technical Efficacy Thesaurus, Application Domain, Technology Topic, Popular Technical Reports.
© 2025 PatSnap. All rights reserved.Legal|Privacy policy|Modern Slavery Act Transparency Statement|Sitemap|About US| Contact US: help@patsnap.com