Piezoelectric six-dimensional force sensor
A six-dimensional force sensor, piezoelectric technology, applied in the direction of measuring force components, etc., to achieve the effect of large measurement range, clear force mapping relationship, and improved response speed and sensitivity
- Summary
- Abstract
- Description
- Claims
- Application Information
AI Technical Summary
Problems solved by technology
Method used
Image
Examples
Embodiment Construction
[0010] The present invention will be further described in detail below in conjunction with the accompanying drawings and embodiments. like figure 1 and figure 2 As shown, the piezoelectric six-dimensional force sensor based on the Stewart structure in the present invention consists of an upper platform 1, a lower platform 2, six ball joints 3 on the upper rod, six upper rods on the connecting rod 4, and six groups of one-dimensional piezoelectric quartz sensors. 5. Six connecting rods, lower rods 6, and six lower rod ball joints 7 are composed. Six upper rod ball joints 3 and six down rod ball joints 7 are fixed on the upper platform 1 by four fixing screws through each ball joint. and the lower platform 2, the diameter of the lower platform 2 is greater than the diameter of the upper platform 1, and the six branch one-dimensional piezoelectric quartz sensors 5 are uniformly connected between the upper and lower platforms 1 and 2 according to a semisymmetric structure, and e...
PUM
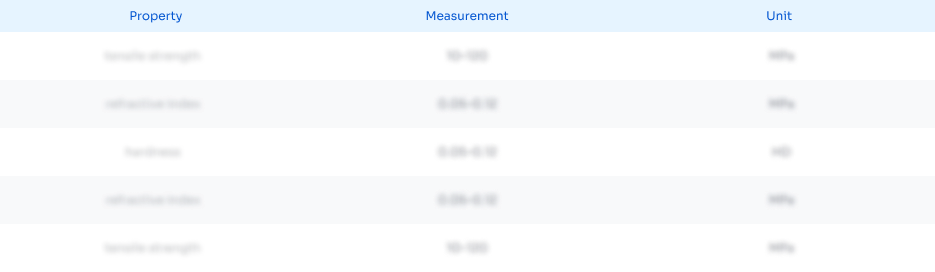
Abstract
Description
Claims
Application Information

- R&D
- Intellectual Property
- Life Sciences
- Materials
- Tech Scout
- Unparalleled Data Quality
- Higher Quality Content
- 60% Fewer Hallucinations
Browse by: Latest US Patents, China's latest patents, Technical Efficacy Thesaurus, Application Domain, Technology Topic, Popular Technical Reports.
© 2025 PatSnap. All rights reserved.Legal|Privacy policy|Modern Slavery Act Transparency Statement|Sitemap|About US| Contact US: help@patsnap.com