Chambered cooling device for sintered ore and pellet ore
A cooling device and pelletizing technology, applied in the field of blast furnace smelting, can solve problems such as insufficient heat exchange, uncooled material column center, uneven discharge, etc., and achieve independent setting of cooling time, multi-point and output Material capacity, the effect of meeting accurate requirements
- Summary
- Abstract
- Description
- Claims
- Application Information
AI Technical Summary
Problems solved by technology
Method used
Image
Examples
Embodiment Construction
[0021] The present invention will be further explained below in conjunction with the accompanying drawings.
[0022] Such as Figures 1 to 3 As shown, a compartment cooling device for sinter and pellets of the present invention includes a feeding system, a feeding valve group, a vertical furnace body, a discharge valve, a secondary cooling chamber 13 and a ventilation pipeline.
[0023] The vertical furnace body includes a furnace shell 3, an inner sleeve 2 is arranged at the center of the furnace shell 3, and an annular interlayer 10 is formed between the inner sleeve 2 and the furnace shell 3, and the annular interlayer 10 is circular or polygonal.
[0024] A feeding valve group is arranged on the top of the annular interlayer 10, and the feeding valve group is connected to the feeding system. The feeding valve group includes a material inlet sealing bell valve 6 , and the feeding system includes a feeding trolley 5 . The upper part of the annular interlayer 10 is provided...
PUM
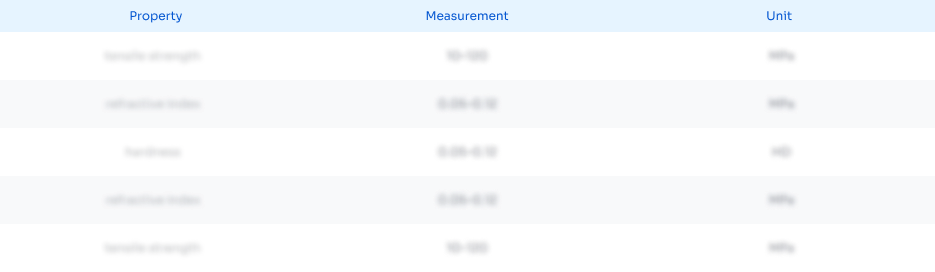
Abstract
Description
Claims
Application Information

- R&D
- Intellectual Property
- Life Sciences
- Materials
- Tech Scout
- Unparalleled Data Quality
- Higher Quality Content
- 60% Fewer Hallucinations
Browse by: Latest US Patents, China's latest patents, Technical Efficacy Thesaurus, Application Domain, Technology Topic, Popular Technical Reports.
© 2025 PatSnap. All rights reserved.Legal|Privacy policy|Modern Slavery Act Transparency Statement|Sitemap|About US| Contact US: help@patsnap.com