A kind of manufacturing method of rotary self-riveting forming motor rotor core
A technology of rotor iron core and motor rotor, which is applied in the manufacture of motor generators, stator/rotor bodies, electromechanical devices, etc. It can solve problems such as the inability to eliminate jumping, reduce the quality of the iron core, and large motor noise and vibration. Mechanical finishing process, improved service life, uniform effect of rotor magnetic circuit
- Summary
- Abstract
- Description
- Claims
- Application Information
AI Technical Summary
Problems solved by technology
Method used
Image
Examples
Embodiment 1
[0055] The illustration of the present embodiment, the adopted material thickness is roughly the bar of d=0.5mm, and the number n=100 of annular rotor punching sheets 1 (the number n of the rotor punching sheets 1 whose sheet thickness is definite is made of rotor iron. The core stack height is determined by the stack height of the rotor core (H = 50mm), and the slots of the rotor core and stator core to be manufactured are matched as follows: the number of guide slots for the rotor core Q = 34, and the stator core The number of embedding slots Z=24.
[0056] Please refer to Picture 1-1 , 1-2 , 1-3, 2-1, 2-2, 2-3, 2-4, 3-1, 3-2, 3-3, 3-4, 4-1, 4-2, 4-3, 4 As shown in -4, the rotor core is formed by continuously punching and riveting 100 ring-shaped rotor punching pieces 1 automatically and continuously on the punching die with continuously conveyed strips. The punching process of the rotor punching 1 includes Sequentially punching the inner circle together with the guide bar ...
Embodiment 2
[0081] The illustration of the present embodiment, the adopted material thickness is roughly the bar of d=0.5mm, and the number n=100 of annular rotor punching sheets 1 (the number n of the rotor punching sheets 1 whose sheet thickness is definite is made of rotor iron. The stack height of the rotor core is determined by the stack height of the rotor core (H = 50mm). The slots of the rotor core and the stator core to be manufactured are matched as follows: The number of slots Z=24.
[0082] Please refer to Figure 5-1 , 5-2 , 5-3, 6-1, 6-2, 6-3, 6-4, 7-1, 7-2, 7-3, 7-4, 8-1, 8-2, 8-3, 8 As shown in -4, the rotor core is formed by continuously punching and riveting 100 ring-shaped rotor punching pieces 1 automatically and continuously on the punching die with continuously conveyed strips. The punching process of the rotor punching 1 includes Sequentially punching the inner circle together with the guide bar grooves 10 evenly spaced, punching the rivets together with the thro...
PUM
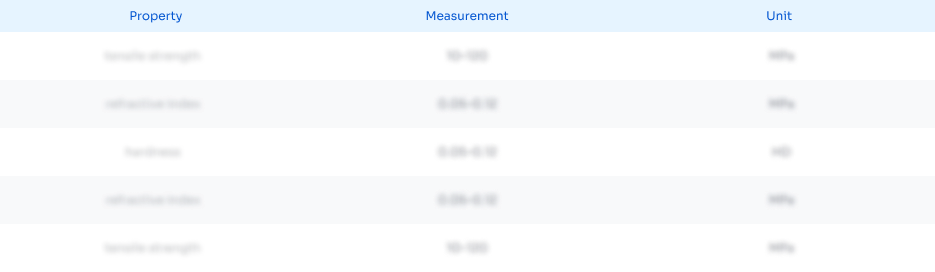
Abstract
Description
Claims
Application Information

- Generate Ideas
- Intellectual Property
- Life Sciences
- Materials
- Tech Scout
- Unparalleled Data Quality
- Higher Quality Content
- 60% Fewer Hallucinations
Browse by: Latest US Patents, China's latest patents, Technical Efficacy Thesaurus, Application Domain, Technology Topic, Popular Technical Reports.
© 2025 PatSnap. All rights reserved.Legal|Privacy policy|Modern Slavery Act Transparency Statement|Sitemap|About US| Contact US: help@patsnap.com