Metal structure fatigue reliability analyzing and optimizing design method based on damage mechanics
A technology of damage mechanics and optimal design, applied in the field of fatigue fracture and damage mechanics, can solve problems such as useless consideration of fatigue performance
- Summary
- Abstract
- Description
- Claims
- Application Information
AI Technical Summary
Problems solved by technology
Method used
Image
Examples
Embodiment
[0081] In order to fully explain the characteristics of the invention, the present invention aims at Figure 5 The shown standard metal fatigue structural part model performs non-probability interval reliability analysis and optimization design based on damage mechanics. The rectangular plate material is LY12CZ aluminum alloy, and the chemical composition of the material is shown in Table 1 below. The initial design dimensions of the plate are 210mm, 100mm, and 10mm in length, width, and diameter of the center hole respectively. The load is 150MPa uniform stress at both ends, and the stress ratio is 0.2. The finite element mesh is divided into Figure 7 Shown. According to the content described in the above invention, the thickness of the plate is taken as the design variable, the reliability is greater than 0.95 as the constraint condition, and the minimum plate quality is the objective function. Image 6 The optimization process of ASA applies the ASA global optimization algo...
PUM
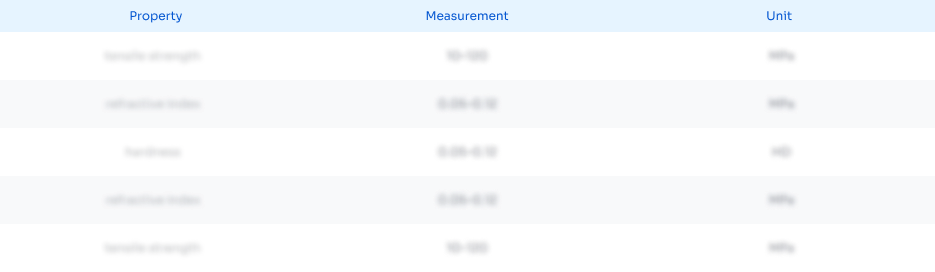
Abstract
Description
Claims
Application Information

- R&D
- Intellectual Property
- Life Sciences
- Materials
- Tech Scout
- Unparalleled Data Quality
- Higher Quality Content
- 60% Fewer Hallucinations
Browse by: Latest US Patents, China's latest patents, Technical Efficacy Thesaurus, Application Domain, Technology Topic, Popular Technical Reports.
© 2025 PatSnap. All rights reserved.Legal|Privacy policy|Modern Slavery Act Transparency Statement|Sitemap|About US| Contact US: help@patsnap.com