Construction Method of Continuous Time System for Displacement Detection of Radial Magnetic Bearing
A technology of time system and displacement detection, which is applied in control system, vector control system, electronic commutation motor control, etc. It can solve the problems of poor detection accuracy and real-time performance of magnetic bearing displacement, restriction of maximum rotational speed of magnetic bearing, difficulty in maintenance, etc.
- Summary
- Abstract
- Description
- Claims
- Application Information
AI Technical Summary
Problems solved by technology
Method used
Image
Examples
Embodiment 1
[0043] Such as figure 1 As shown, this embodiment 1 provides a method for constructing a continuous-time system for radial magnetic bearing displacement detection, including the following steps:
[0044] Step S1, calculating the levitation force on the rotor in the directions of the three magnetic poles;
[0045] Step S2, establishing a continuous time system.
[0046] Specifically, the method for calculating the levitation force on the rotor in the direction of the three magnetic poles in the step S1 includes:
[0047] Step S11, calculate the magnetic flux of the air gap of each magnetic pole, which is shown in formula (1):
[0048]
[0049] In formula (1), Φ A 、Φ B 、Φ C are the magnetic fluxes corresponding to the air gaps of the three-phase magnetic poles; N 3 is the equivalent number of turns in the x and y directions; R A , R B , R C are the reluctances of the air gaps of the three poles; i A i B i C are the currents flowing through the three poles respecti...
Embodiment 2
[0095] On the basis of Embodiment 1, Embodiment 2 provides a radial magnetic bearing displacement detection method, including:
[0096] According to the continuous time system, the radial displacement output signal and rotational speed signal of the rotor in the x and y directions are obtained, and the continuous time system is discretized to realize the volumetric Kalman filter algorithm to extract the displacement information of the rotor.
[0097] Wherein, the method for extracting the displacement information of the rotor by the volumetric Kalman filter algorithm includes: generating the current I by the volumetric Kalman filter according to the voltage source inverter A , I B , I C Extracted current signal x cub and y cub , and obtain the displacement output signal x of the radial magnetic bearing in the x and y directions through the observer est and y est , where the displacement output signal x est and y est It also represents the displacement information of the...
Embodiment 3
[0101] On the basis of Embodiment 1, Embodiment 3 provides a displacement detection method for a radial magnetic bearing.
[0102] The radial magnetic bearing displacement detection method includes: building a feedback loop through a volumetric Kalman filter to adjust the current generated by the voltage source inverter to drive the magnetic bearing to achieve closed-loop stable suspension.
[0103] Specifically, a feedback loop is constructed through a volumetric Kalman filter, namely
[0104] The current I is generated by the volumetric Kalman filter according to the voltage source inverter A , I B , I C Extracted current signal x cub and y cub , and obtain the displacement output signal x of the radial magnetic bearing in the x and y directions through the observer est and y est , with a given reference position signal x ref and y ref For comparison, after the obtained result is processed by the first P controller, it is respectively compared with the speed signal v...
PUM
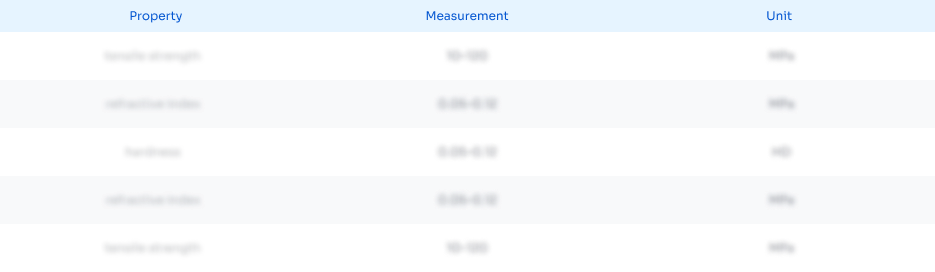
Abstract
Description
Claims
Application Information

- R&D Engineer
- R&D Manager
- IP Professional
- Industry Leading Data Capabilities
- Powerful AI technology
- Patent DNA Extraction
Browse by: Latest US Patents, China's latest patents, Technical Efficacy Thesaurus, Application Domain, Technology Topic, Popular Technical Reports.
© 2024 PatSnap. All rights reserved.Legal|Privacy policy|Modern Slavery Act Transparency Statement|Sitemap|About US| Contact US: help@patsnap.com