Water-based dry method foaming raincoat leather and preparation method thereof
A technology of raincoat leather and dry method, which is applied in the direction of textiles and papermaking, can solve the problems of strength and water pressure resistance, damage to human health by plasticizers, and damage to human health, etc., to improve water resistance, strong water pressure resistance, The effect of high environmental standards
- Summary
- Abstract
- Description
- Claims
- Application Information
AI Technical Summary
Problems solved by technology
Method used
Image
Examples
Embodiment 1
[0046] (1) Preparation of slurry for surface layer, middle layer, foam layer and bottom layer:
[0047] (1) Preparation of the slurry of the surface layer:
[0048] Take 100kg of water-based polyurethane resin KTT628F (produced by Hefei Ketian Chemical Co., Ltd.), 6kg of water-based color paste, 0.8kg of RHEOLATE208 water-based thickener, 0.6kg of TEGO902W defoamer and 0.6kg of BD-3376 leveling agent Add to the mixer one by one, seal and vacuumize, and then stir until the slurry is evenly dispersed.
[0049] (2) Preparation of the slurry in the middle layer:
[0050] Take 100kg of water-based polyurethane resin KTM797 (produced by Hefei Ketian Chemical Co., Ltd.), 4kg of water-based color paste, 1kg of RHEOLATE208 water-based thickener, 0.5kg of TEGO902W defoamer and 0.5kg of BD-3376 leveling agent in order Add to the mixer, seal and vacuum, then stir until the slurry is evenly dispersed.
[0051] (3) Preparation of the slurry of the foam layer:
[0052] Get 400kg water-ba...
Embodiment 2
[0062] (1) Preparation of slurry for surface layer, middle layer, foam layer and bottom layer:
[0063] (1) Preparation of the slurry of the surface layer:
[0064] Take 100kg of water-based polyurethane resin KTT628F (produced by Hefei Ketian Chemical Co., Ltd.), 8kg of water-based color paste, 1.2kg of RHEOLATE208 water-based thickener, 0.8kg of TEGO902W defoamer and 1.0kg of BD-3376 leveling agent Add to the mixer one by one, seal and vacuumize, and then stir until the slurry is evenly dispersed.
[0065] (2) Preparation of the slurry in the middle layer:
[0066] Take 100kg of water-based polyurethane resin KTM797 (produced by Hefei Ketian Chemical Co., Ltd.), 6kg of water-based color paste, 0.6kg of RHEOLATE208 water-based thickener, 0.9kg of TEGO902W defoamer and 0.9kg of BD-3376 leveling agent Add to the mixer one by one, seal and vacuumize, and stir until the slurry is evenly dispersed.
[0067] (3) Preparation of the slurry of the foam layer:
[0068] Get 400kg wa...
Embodiment 3
[0078] (1) Preparation of slurry for surface layer, middle layer, foam layer and bottom layer:
[0079] (1) Preparation of the slurry of the surface layer:
[0080] Take 100kg of water-based polyurethane resin KTT628F (produced by Hefei Ketian Chemical Co., Ltd.), 10kg of water-based color paste, 1.2kg of RHEOLATE208 water-based thickener, 1.5kg of TEGO902W defoamer and 1.3kg of BD-3376 leveling agent Add to the mixer one by one, seal and vacuumize, and then stir until the slurry is evenly dispersed.
[0081] (2) Preparation of the slurry in the middle layer:
[0082] Take 100kg of water-based polyurethane resin KTM797 (produced by Hefei Ketian Chemical Co., Ltd.), 8kg of water-based color paste, 1.5kg of RHEOLATE208 water-based thickener, 1.2kg of TEGO902W defoamer and 1.2kg of BD-3376 leveling agent Add to the mixer one by one, seal and vacuumize, and stir until the slurry is evenly dispersed.
[0083] (3) Preparation of the slurry of the foam layer:
[0084] Get 400kg w...
PUM
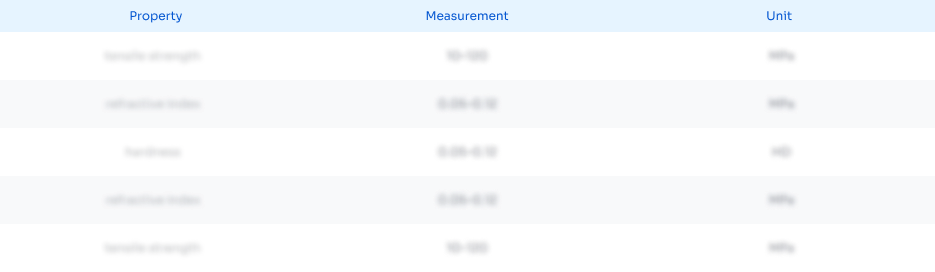
Abstract
Description
Claims
Application Information

- Generate Ideas
- Intellectual Property
- Life Sciences
- Materials
- Tech Scout
- Unparalleled Data Quality
- Higher Quality Content
- 60% Fewer Hallucinations
Browse by: Latest US Patents, China's latest patents, Technical Efficacy Thesaurus, Application Domain, Technology Topic, Popular Technical Reports.
© 2025 PatSnap. All rights reserved.Legal|Privacy policy|Modern Slavery Act Transparency Statement|Sitemap|About US| Contact US: help@patsnap.com