Method for conducting molten iron desulphurization through AOD
A technology for desulfurization and desilication of molten iron, applied in the direction of improving process efficiency, etc., can solve the problems of increased capital construction investment, low casual benefits, low utilization rate of pre-treatment devices outside the furnace, etc., and achieves reduced investment costs, flexible organization, and flexibility. production effect
- Summary
- Abstract
- Description
- Claims
- Application Information
AI Technical Summary
Problems solved by technology
Method used
Examples
Embodiment 1
[0021] Embodiment 1: The specific process of the method for using AOD to desulfurize molten iron is as follows.
[0022] (1) Initial conditions: the amount of molten iron is 45 tons, the initial temperature of the molten iron is 1150°C, the initial sulfur content of the molten iron is 470ppm, and the initial silicon content of the molten iron is 0.97wt%.
[0023] (2) Desulfurization process and calculation process: the total flow of oxygen is 1.96m per ton of iron 3 / min, among which, the oxygen flow rate of the top gun is 80m 3 / min, side gun oxygen flow 8m 3 / min, side gun nitrogen flow 12m 3 / minute;
[0024] Calculate the desiliconization amount according to the target molten iron temperature of 1380°C = (1380-1150) / 250*45*10=414 (kg);
[0025] Corresponding oxygen blowing volume=414*0.98=405.7m 3 ;
[0026] Corresponding lime addition = 414*2.14*1.8 / 0.88=1812.2 (kg);
[0027] Corresponding fluorite addition amount=1812.2*0.25=453 (kg);
[0028] Corresponding oxyge...
Embodiment 2
[0030] Embodiment 2: The specific process of the method for using AOD to desulfurize molten iron is as follows.
[0031] (1) Initial conditions: the amount of molten iron is 45 tons, the initial temperature of the molten iron is 1145°C, the initial sulfur content of the molten iron is 480ppm, and the initial silicon content of the molten iron is 0.96wt%.
[0032] (2) Desulfurization process and calculation process: the total flow of oxygen is 1.89m per ton of iron 3 / min, among which, the oxygen flow rate of the top gun is 80m 3 / min, side gun oxygen flow 8m 3 / min, side gun nitrogen flow 20m 3 / minute;
[0033] According to the target molten iron temperature of 1400°C, calculate the desiliconization amount = (1400-1145) / 280*45*10=409.8 (kg);
[0034] Corresponding oxygen blowing volume=409.8*0.90=368.8m 3 ;
[0035] Corresponding lime addition = 409.8*2.14*1.7 / 0.88=1694.2 (kg);
[0036] Corresponding fluorite addition amount=1694.2*0.30=508.3 (kg);
[0037] Correspond...
Embodiment 3
[0039] Embodiment 3: The specific process of the method of using AOD to desulfurize molten iron is as follows.
[0040] (1) Initial conditions: the amount of molten iron is 45 tons, the initial temperature of the molten iron is 1152°C, the initial sulfur content of the molten iron is 476ppm, and the initial silicon content of the molten iron is 0.98wt%.
[0041] (2) Desulfurization process and calculation process: the total flow rate of oxygen is 2.3m per ton of iron 3 / min, among which, the oxygen flow rate of the top gun is 90m 3 / min, side gun oxygen flow 10m 3 / min, side gun nitrogen flow 20m 3 / minute;
[0042] Calculate the desiliconization amount according to the target molten iron temperature of 1430°C = (1430-1152) / 260*45*10=481.2 (kg);
[0043] Corresponding oxygen blowing volume=481.2*1.0=481.2m 3 ;
[0044] Corresponding lime addition = 481.2*2.14*1.8 / 0.88=2106.3 (kg);
[0045] Corresponding fluorite addition amount=2106.3*0.20=421.3 (kg);
[0046] Correspo...
PUM
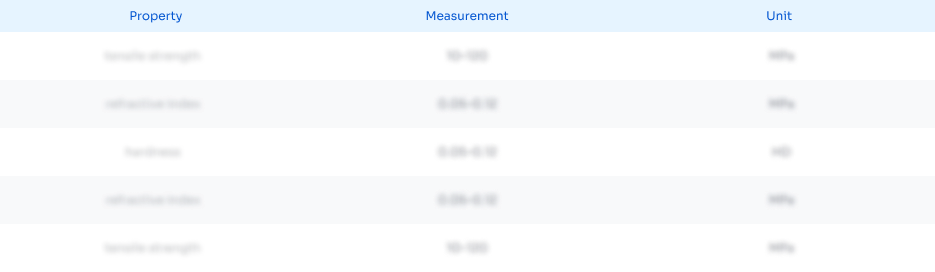
Abstract
Description
Claims
Application Information

- R&D
- Intellectual Property
- Life Sciences
- Materials
- Tech Scout
- Unparalleled Data Quality
- Higher Quality Content
- 60% Fewer Hallucinations
Browse by: Latest US Patents, China's latest patents, Technical Efficacy Thesaurus, Application Domain, Technology Topic, Popular Technical Reports.
© 2025 PatSnap. All rights reserved.Legal|Privacy policy|Modern Slavery Act Transparency Statement|Sitemap|About US| Contact US: help@patsnap.com