Ultrafine dibutyltin oxide and preparation method thereof
A technology of dibutyl tin dichloride and fine dibutyl, which is applied in chemical instruments and methods, organic chemistry, tin organic compounds, etc., and can solve problems such as obvious coating defects, uneven particles, and poor catalytic effect , to achieve the effect of low concentration of soluble ions and fine and uniform particles
- Summary
- Abstract
- Description
- Claims
- Application Information
AI Technical Summary
Problems solved by technology
Method used
Examples
Embodiment 1
[0014] Weigh 24g of sodium hydroxide solid into a 500ml four-neck flask, dissolve with 150g of water, add 4 drops of surfactant for later use, weigh 80g of dibutyltin dichloride into a beaker and heat to 60°C, slowly introduce Atomization was carried out in an ultrasonic atomizer, the flask was turned on to stir, and the atomized gas flow was introduced into a four-necked flask 1 cm below the lye liquid surface through a glass tube for the first reaction, and the reaction temperature was controlled at 60°C. After the reaction was completed, the water was removed by suction filtration, and then 10 g of ammonia water was added to carry out the second or third reaction. Washing with deionized water, suction filtration, and drying to finally obtain 63.5 g of dibutyltin oxide product. The test indicators are as follows: Sn: 47.25%; Cl: 0.0120%; moisture 98%.
Embodiment 2
[0016] Weigh 30g of sodium hydroxide solid into a 1000ml beaker, dissolve it with 200g of water, add 6 drops of surfactant, turn on the stirrer; weigh 100g of dibutyltin dichloride, heat to 70°C, and pass through the airflow atomizer Spray it into a beaker, and control the temperature to 70°C for the first reaction. After the reaction was completed, the water was removed by suction filtration, and then 10 g of ammonia water was added to carry out the second or third reactions. Washing with deionized water, suction filtration, and drying to finally obtain 80.1 g of dibutyltin oxide product. The test indicators are as follows: Sn: 47.36%; Cl: 0.0090%; moisture 95%.
Embodiment 3
[0018] Weigh 10g of sodium carbonate solid and put it into a 500ml four-necked flask, dissolve it with 200g of water, add 80g of ammonia water with a concentration of 20%, add 6 drops of surfactant, turn on the stirrer, and weigh 100g of dibutyltin dichloride Heat it to 65°C, spray it into a beaker through an airflow atomizer, and control the temperature to 45°C for the first reaction. After the reaction was completed, the water was removed by suction filtration, and then 10 g of ammonia water was added to carry out the second or third reactions. Washing with deionized water, suction filtration, and drying to finally obtain 79.6g of dibutyltin oxide product. The test indicators are as follows: Sn: 47.23%; Cl: 0.0076%; moisture 98%.
PUM
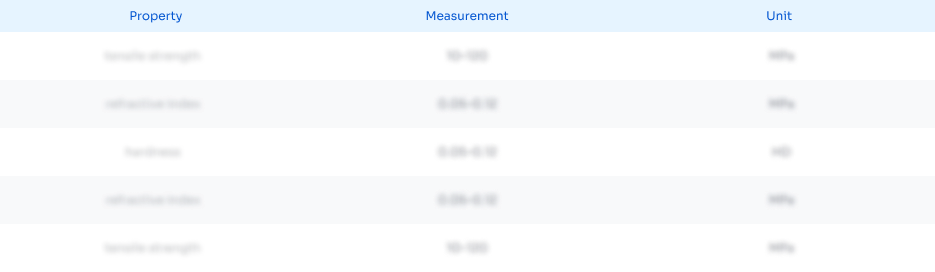
Abstract
Description
Claims
Application Information

- R&D
- Intellectual Property
- Life Sciences
- Materials
- Tech Scout
- Unparalleled Data Quality
- Higher Quality Content
- 60% Fewer Hallucinations
Browse by: Latest US Patents, China's latest patents, Technical Efficacy Thesaurus, Application Domain, Technology Topic, Popular Technical Reports.
© 2025 PatSnap. All rights reserved.Legal|Privacy policy|Modern Slavery Act Transparency Statement|Sitemap|About US| Contact US: help@patsnap.com