Method for preparing cyclohexanol by hydrolyzing cyclohexyl formate
A technology of cyclohexyl formate and cyclohexanol, which is applied in the chemical industry, can solve problems such as catalyst loading and replacement difficulties, and reduce the reaction rate, and achieve large-scale industrial production, flexible operation control, and short process flow.
- Summary
- Abstract
- Description
- Claims
- Application Information
AI Technical Summary
Problems solved by technology
Method used
Image
Examples
Embodiment 1
[0034] When the number of knapsack reactors is 1, with cyclohexyl formate and water as raw materials, adopt such as figure 1 Said technological process hydrolyzes and prepares cyclohexanol. The total plate number of described rectifying tower is 16 trays (reaction rectification area tray number 1, stripping area tray number 15); Rectification tower operating pressure is 15kPa; Tower diameter is 0.09m The first knapsack reactor was equipped with 700 g (the catalyst loading was 47.9% of the total mass of cyclohexyl formate and water freshly fed per hour) ion exchange resin Amberlyst 15. The volume of the reactor is 20L. Cyclohexyl formate and water are continuously fed into the first knapsack reactor according to the molar ratio of 1:1. The feed flow rate is 10mol / h. The ion exchange resin Amberlyst 15 is used as the acidic catalyst. At normal pressure, the reaction temperature is 60°C, the reaction liquid enters the reactive distillation zone of the rectification tower, the ga...
Embodiment 2
[0038] The number of knapsack reactors is 2, and the acidic catalyst is acidic molecular sieve HZSM-5, and the loading capacity of the first knapsack reactor is 350g (catalyst loading in the first knapsack reactor is 1 / 2 of fresh feed per hour. 24.0% of cyclohexyl formate and water gross mass), the reactor volume is 20L; The filling capacity of the second knapsack reactor is 300g (catalyst loading is the fresh charge per hour in the second knapsack reactor 20.5% of the total mass of cyclohexyl formate and water), the reactor volume is 20L; the total number of trays in the rectification tower is 13 (the number of trays in the reaction distillation area is 5, and the number of trays in the stripping area is 8) , The operating pressure of the reactive distillation tower is 10kPa, and the diameter of the distillation tower is 0.12m.
[0039] Water and cyclohexyl formate are fed in a molar ratio of 1:1, and the feed flow rate is 10mol / h; cyclohexyl formate is continuously fed into ...
Embodiment 3
[0044] The number of knapsack reactors is 2, and the acidic catalyst is acidic ion exchange resin D072H, and the loading capacity of the first knapsack reactor is 450g (catalyst loading capacity is 1 / 2 of fresh feed per hour in the first knapsack reactor). Cyclohexyl formate and 30.8% of the total mass of water), the reactor volume is 25L; the loading capacity of the second knapsack reactor is 350g (catalyst loading is 1 / 2 of fresh feed per hour in the second knapsack reactor 24.0% of the total mass of cyclohexyl formate and water), the reactor volume is 20L; the total number of trays in the rectification tower is 12 (the number of trays in the reaction distillation zone is 4, and the number of trays in the stripping zone is 8) , The operating pressure of the reactive distillation column is 10kPa, and the diameter of the distillation column is 0.09m.
[0045] Water and cyclohexyl formate are fed in a molar ratio of 1:1, and the feed flow rate is 10mol / h; cyclohexyl formate is ...
PUM
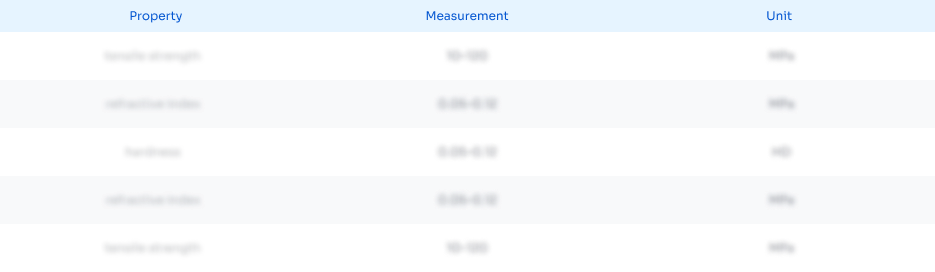
Abstract
Description
Claims
Application Information

- R&D
- Intellectual Property
- Life Sciences
- Materials
- Tech Scout
- Unparalleled Data Quality
- Higher Quality Content
- 60% Fewer Hallucinations
Browse by: Latest US Patents, China's latest patents, Technical Efficacy Thesaurus, Application Domain, Technology Topic, Popular Technical Reports.
© 2025 PatSnap. All rights reserved.Legal|Privacy policy|Modern Slavery Act Transparency Statement|Sitemap|About US| Contact US: help@patsnap.com