Preparation method of polymethyl-methacrylate-based compatilizer
The technology of polymethyl methacrylate and hydroxyl-terminated polyacrylate is applied in the field of preparation based on polymethyl methacrylate compatibilizer, can solve the problems of low grafting rate and the like, and achieves simple preparation method and grafting density. Adjustable, chain-length controllable effects
- Summary
- Abstract
- Description
- Claims
- Application Information
AI Technical Summary
Problems solved by technology
Method used
Image
Examples
Embodiment 1
[0020] (1) Preparation of hydroxyl-terminated polymethylacrylate (design molecular weight 1000)
[0021] Add 20.00g (0.2323mol) of methyl acrylate, 4.7884g (20.026mmol) of initiator α-bromoisobutyrate 4.7884g (20.026mmol) of methyl acrylate, CuBr 2 0.02082g (0.09293mmol) and pentamethyldivinyltriamine PMDETA 0.3221g (1.8585mmol), reducing agent stannous octoate Sn (EH) 2 0.7529g (1.8585mmol) and 10.00g of solvent toluene, after mixing evenly, blow nitrogen gas, react in 70°C oil bath for 210min, stop the reaction after the conversion rate reaches 81%, the product passes through the neutral alumina column, precipitates and bakes Dry and set aside.
[0022] (2) Preparation of hydroxyl-containing polymethyl methacrylate
[0023] In a 500ml reaction flask equipped with toluene, slowly dropwise add a mixed monomer solution of 80g (0.7990mol) of methyl methacrylate, 20g (0.1722mol) of hydroxyethyl acrylate and 0.5g of dibenzoyl peroxide, at 85°C After 6 hours of reaction, the t...
Embodiment 2
[0027] (1) Preparation of hydroxyl-terminated polyethylacrylate (design molecular weight 3000)
[0028] Add 20.00 g (0.1998 mol) of ethyl acrylate, 1.5941 g (6.6667 mmol) of initiator α-bromoisobutyrate 1.5941 g (6.6667 mmol) of ethyl acrylate, CuBr 2 0.01790g (0.0799mmol) and PMDETA 0.2759g (1.5981mmol), reducing agent Sn(EH) 2 Mix 0.6474g (1.5981mmol) and toluene 10g, mix well and then bubble with nitrogen, react in an oil bath at 75°C for 255min, stop when the conversion rate reaches 86%, pass the product through a neutral alumina column, precipitate with methanol, and dry .
[0029] (2) Preparation of hydroxyl-containing polymethyl methacrylate
[0030] In a 500ml reaction flask equipped with toluene, slowly dropwise add a mixed monomer solution of 80g (0.7990mol) of methyl methacrylate, 5g (0.04306mol) of hydroxyethyl acrylate and 0.255g of dibenzoyl peroxide, at 85°C After 6 hours of reaction, the temperature was lowered and the material was discharged, and the prod...
Embodiment 3
[0034] (1) Preparation of hydroxyl-terminated polybutylacrylate (design molecular weight 5000)
[0035] Add 20.00 g (0.1560 mol) of butyl acrylate, 0.9564 g (4.000 mmol) of initiator α-bromoisobutyrate 0.9564 g (4.000 mmol) of butyl acrylate, CuBr 2 0.01398g (0.06242mmol) and PMDETA 0.2163g (1.2483mmol), reducing agent Sn(EH) 2 0.5057g (1.2483mmol) and 15g of toluene, mixed evenly, nitrogen bubbling, reacted in an oil bath at 80°C for 215min, stopped when the conversion rate reached 85%, and the product passed through a neutral alumina column and dried with methanol precipitation.
[0036] (2) Preparation of hydroxyl-containing polymethyl methacrylate
[0037]In a 500ml reaction flask equipped with toluene, slowly dropwise add a mixed monomer solution of 80g (0.7990mol) of methyl methacrylate, 15g (0.1292mol) of hydroxyethyl acrylate and 0.285g of dibenzoyl peroxide, at 85°C After 7 hours of reaction, the temperature was lowered and the material was discharged, and the pro...
PUM
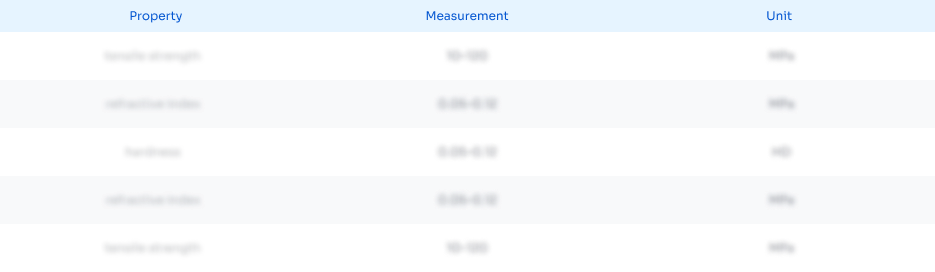
Abstract
Description
Claims
Application Information

- Generate Ideas
- Intellectual Property
- Life Sciences
- Materials
- Tech Scout
- Unparalleled Data Quality
- Higher Quality Content
- 60% Fewer Hallucinations
Browse by: Latest US Patents, China's latest patents, Technical Efficacy Thesaurus, Application Domain, Technology Topic, Popular Technical Reports.
© 2025 PatSnap. All rights reserved.Legal|Privacy policy|Modern Slavery Act Transparency Statement|Sitemap|About US| Contact US: help@patsnap.com