Preparation method of high-strength waterproof composite coal briquette adhesive
A compound type and adhesive technology, which is applied in the petroleum industry, solid fuel, fuel, etc., can solve the problems that it is difficult to meet the transportation strength and waterproof requirements of coal briquettes, reduce lime activity, etc., and achieve good impact resistance and hydrophilicity Strong, high thermal strength effect
- Summary
- Abstract
- Description
- Claims
- Application Information
AI Technical Summary
Problems solved by technology
Method used
Examples
Embodiment 1
[0028] Take 5.52kg of magnesium oxide, 1.49kg of high-energy activator, 0.168kg of surfactant, and 12.32kg of bituminous coal in weight proportions, respectively pulverize and sieve, and weigh the ingredients according to the weight percentage of the components, and weigh the biomass fibers according to the proportions, and take water Put 27.3kg in a container, add the biomass fiber into the water, stir it with a stirrer after it fully absorbs water, so that the biomass fiber is well dispersed in the water; then put the weighed components into powder Add, and stir while adding, until it is evenly mixed.
[0029] Crush the anthracite pulverized coal to less than 3.0mm, mix the prepared binder with the anthracite coal powder at a weight ratio of 21:79, and mix 79kg of anthracite powder, fully stir, grind, and stand for 8 hours before forming On the machine, use 20MPa pressure to press into a briquette with a diameter of 40mm and a weight of 40g, and then dry it at a temperature ...
Embodiment 2
[0031] Get 5.04kg of magnesium oxide 24%, 1.05kg of activator, 2.52kg of biomass fiber, 0.105kg of surfactant, 12.285kg of bituminous coal, 23.1kg of water, and the manufacturing steps are as in Example 1.
[0032] Crush the anthracite pulverized coal to less than 3.0mm, mix the prepared binder with the anthracite coal powder at a weight ratio of 21:79, and mix 79kg of anthracite powder, fully stir, grind, and stand for 8 hours before forming On the machine, use 20MPa pressure to press into a briquette with a diameter of 40mm and a weight of 40g, and then dry it at a temperature of about 100°C for 3 hours to obtain the finished briquette. After testing, the cold compressive strength of the shaped coal is higher than 4.2MPa, and the hot compressive strength is above 1.2MPa. The shaped coal falls freely from a height of 2m three times continuously onto a thick steel plate without breaking. The stability index exceeds 81%, and the wear resistance index reaches more than 96%. The ...
Embodiment 3
[0034] Get 7.14kg of magnesium oxide, 1.68kg of activator, 1.26kg of biomass fiber, 0.21kg of surfactant, 10.71kg of bituminous coal, and 25.2kg of water. The manufacturing steps are as in Example 1.
[0035] Crush the anthracite pulverized coal to less than 3.0mm, mix the prepared binder with the anthracite coal powder at a weight ratio of 21:79, and mix 79kg of anthracite powder, fully stir, grind, and stand for 8 hours before forming On the machine, use 20MPa pressure to press into a briquette with a diameter of 40mm and a weight of 40g, and then dry it at a temperature of about 100°C for 3 hours to obtain the finished briquette. After testing, the cold compressive strength of the briquette is higher than 4.13MPa, and the hot compressive strength is over 1.14MPa. The briquette is free-falled from a height of 2m for 3 consecutive times onto a thick steel plate without breaking. The stability index exceeds 88%, and the wear resistance index reaches more than 92%. The fixed ca...
PUM
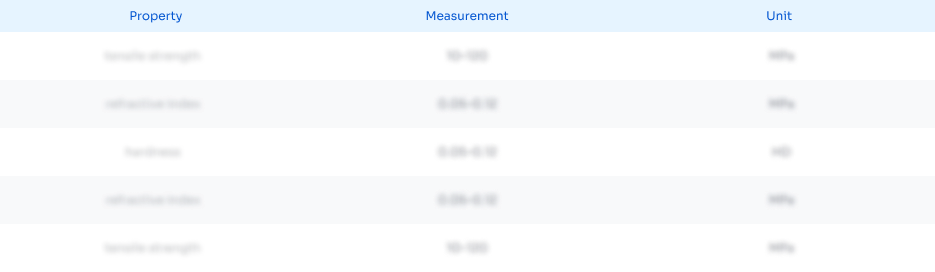
Abstract
Description
Claims
Application Information

- R&D
- Intellectual Property
- Life Sciences
- Materials
- Tech Scout
- Unparalleled Data Quality
- Higher Quality Content
- 60% Fewer Hallucinations
Browse by: Latest US Patents, China's latest patents, Technical Efficacy Thesaurus, Application Domain, Technology Topic, Popular Technical Reports.
© 2025 PatSnap. All rights reserved.Legal|Privacy policy|Modern Slavery Act Transparency Statement|Sitemap|About US| Contact US: help@patsnap.com