A new type of aluminum fuel tank and its production method
A fuel tank, a new type of technology, applied to the layout combined with the fuel supply of internal combustion engines, power devices, vehicle components, etc., can solve the problems of high production failure rate of fuel tanks, unreasonable fuel tank structure, heavy welding workload, etc. , to achieve the effect of improving defect rate, increasing production tempo and improving production efficiency
- Summary
- Abstract
- Description
- Claims
- Application Information
AI Technical Summary
Problems solved by technology
Method used
Image
Examples
Embodiment 1
[0026] Embodiment 1: (1) Forming of the first body A: Select the aluminum alloy sheet and cut it into the required size of the first body A, mark it at a fixed point, use a box punching machine to punch the oil tank hole, and punch the hole with a hydraulic oil pressure of 11Mpa. The edge machine shifts the edge of the plate 50mm inward to fold out the first beveled section A2 and the first joint section A3 at a bending angle of 30°, and then uses a square oil tank forming machine to fold and close the plate, and the plate feeding speed is 4000mm / Min, the pressure holding time for each fold is 5S, after sealing, MIG welding is performed on the edge of the plate joint by a straight seam welding machine, the welding speed is 3000mm / min, the welding current is 60A, the wire feeding speed is 4m / s, the welding torch height is 12mm, the welding torch The angle is 70°, the flow rate of argon gas is 12L / min, the weld seam width is 9mm, and the residual height is 0.5-1mm. Clean up the we...
Embodiment 2
[0032] Embodiment 2: (1) Forming of the first body A: Select the aluminum alloy plate and cut it into the required size of the first body A, mark it at a fixed point, use a box punching machine to punch the oil tank hole, and punch the hole with a hydraulic oil pressure of 13Mpa. The edge machine folds the first hypotenuse section A2 and the first joint section A3 at the position where the edge of the sheet is offset inward by 55mm, and the bending angle is 45°, and then the sheet is folded and closed with a square fuel tank forming machine, and the sheet feeding speed is 4000mm / Min, the pressure holding time for each fold is 5S, after sealing, MIG welding is performed on the edge of the plate joint by a straight seam welding machine, the welding speed is 3000-3200mm / min, the welding current is 60-65A, and the wire feeding speed is 4.2m / s. The height of the welding torch is 15mm, the angle of the welding torch is 75°, the flow rate of argon gas is 14L / min, the width of the wel...
Embodiment 3
[0038] Embodiment 3: (1) Forming of the first body A: Select the aluminum alloy plate and cut it into the required size of the first body A, mark it at a fixed point, use a box punching machine to punch the oil tank hole, and punch the hole with a hydraulic oil pressure of 15Mpa. The edge machine shifts the edge of the plate 60mm inward to fold out the first beveled section A2 and the first joint section A3, with a bending angle of 60°, and then uses a square fuel tank forming machine to fold and close the plate, and the plate feeding speed is 4000mm / Min, the pressure holding time for each fold is 5S, after sealing, MIG welding is performed on the edge of the plate joint by a straight seam welding machine, the welding speed is 3200mm / min, the welding current is 65A, the wire feeding speed is 4.3m / s, and the welding torch height is 18mm. The angle of the welding torch is 85°, the flow rate of argon gas is 16L / min, the width of the weld is 11mm, and the reinforcement height is 0...
PUM
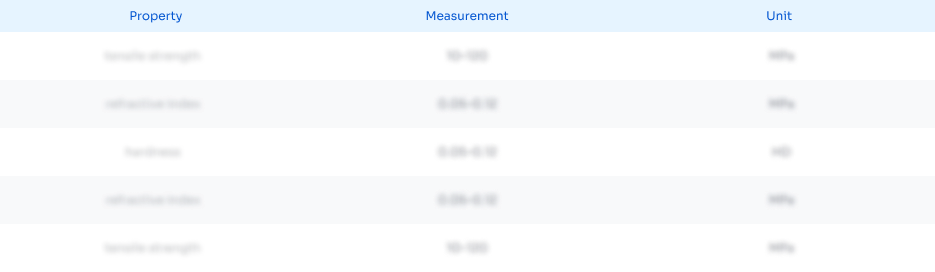
Abstract
Description
Claims
Application Information

- Generate Ideas
- Intellectual Property
- Life Sciences
- Materials
- Tech Scout
- Unparalleled Data Quality
- Higher Quality Content
- 60% Fewer Hallucinations
Browse by: Latest US Patents, China's latest patents, Technical Efficacy Thesaurus, Application Domain, Technology Topic, Popular Technical Reports.
© 2025 PatSnap. All rights reserved.Legal|Privacy policy|Modern Slavery Act Transparency Statement|Sitemap|About US| Contact US: help@patsnap.com