Low-cost high-forming-efficiency injection mold
An injection mold, high molding technology, applied in the field of injection molds with low cost and high molding efficiency, can solve the problems of scorch marks, flow marks, profit reduction, product production cycle can not be effectively reduced, etc., to improve cooling speed, Improve the effect of injection molding second mold
- Summary
- Abstract
- Description
- Claims
- Application Information
AI Technical Summary
Problems solved by technology
Method used
Image
Examples
Embodiment
[0019] Such as figure 1 As shown, a low-cost and high-efficiency injection mold is used for molding injection molded parts 3. The injection mold includes a fixed mold and a movable mold, and the fixed mold is provided with a first male mold core 1 and the second male mold core 2, the first male mold core 1 is detachably connected to the second male mold core 2, and the first male mold core 1 is connected to the injection molded part 3 to be formed.
[0020] The first male mold core 1 and the second male mold core 2 are fixed by screws and combined and polished together. A gap for gas discharge is provided between the first male mold core 1 and the second male mold core 2 . The second male mold core 2 is provided with a cooling water inlet channel 21 and a drainage channel 22 communicating with the first male mold core 1; the cooling water enters from the water inlet channel of the second male mold core 2 and passes through the first male core After the mold core 1 evenly cir...
PUM
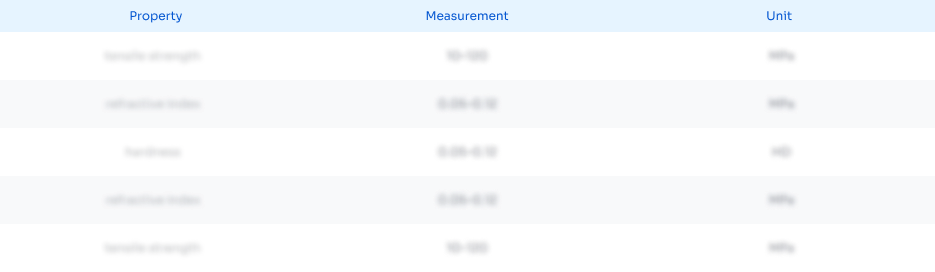
Abstract
Description
Claims
Application Information

- R&D
- Intellectual Property
- Life Sciences
- Materials
- Tech Scout
- Unparalleled Data Quality
- Higher Quality Content
- 60% Fewer Hallucinations
Browse by: Latest US Patents, China's latest patents, Technical Efficacy Thesaurus, Application Domain, Technology Topic, Popular Technical Reports.
© 2025 PatSnap. All rights reserved.Legal|Privacy policy|Modern Slavery Act Transparency Statement|Sitemap|About US| Contact US: help@patsnap.com