Novel gold-based composite electrical brush material and preparation method thereof
A brush and gold-based technology, which is applied in the field of new gold-based composite brush materials and their preparation, can solve the problems of reducing comprehensive performance, high resource demand, and increasing pollution costs.
- Summary
- Abstract
- Description
- Claims
- Application Information
AI Technical Summary
Problems solved by technology
Method used
Examples
Embodiment 1
[0024] Example 1 The mass fraction of Ag content in the cladding material of the composite material of the present invention is about 20%, the mass fraction of Cu content is about 10%, Au is the balance, and the mass fraction of Cu content in the core material is 85%, Ni The mass fraction of the Sn content is 9%, and the mass fraction of the Sn content is 6%. The gold-based alloy and the copper-based alloy are smelted separately under the protection of Ar gas, and cast in a graphite mold. The processing deformation of the ingot section shrinkage rate is guaranteed to be 30% by forging. The middle of the gold-based alloy ingot is punched and annealed at 700 ° C 1 hour, and drawn into a thin tube with an outer diameter of Φ6mm and a wall thickness of 1mm. The copper-based alloy was annealed at 800°C for 1 hour and then directly drawn to Φ4mm. The two alloys were ultrasonically cleaned in alcohol, and then the gold alloy tube sleeve On the outer layer of the copper alloy rod, it ...
Embodiment 2
[0025] Example 2 The mass fraction of Ag in the cladding material of the composite material of the present invention is about 35%, the mass fraction of Cu is about 5%, Au is the balance, and the core material is the same as in Example 1. The gold-based alloy and the copper-based alloy are smelted separately under the protection of Ar gas, and cast in graphite molds. The processing deformation of the ingot section shrinkage rate is guaranteed to be 35% by forging. The center of the gold-based alloy ingot is punched and annealed at 700 ° C 1 hour, and drawn into a thin tube with an outer diameter of Φ6mm and a wall thickness of 1mm. The copper-based alloy was annealed at 800°C for 1 hour and then directly drawn to Φ4mm. The two alloys were ultrasonically cleaned in alcohol, and then the gold alloy tube sleeve On the outer layer of the copper alloy rod, it is annealed at 700°C for 2 hours; it is forged by precision swaging, the deformation is controlled at about 25%, and then draw...
Embodiment 3
[0026] Example 3 The mass fraction of Ag in the cladding material of the composite material of the present invention is about 5%, the mass fraction of Cu is about 35%, Au is the balance, and the core material is the same as in Example 1. The gold-based alloy and the copper-based alloy are smelted separately under the protection of Ar gas, and cast in graphite molds. The processing deformation of the ingot section shrinkage rate is guaranteed to be 25% by forging. The center of the gold-based alloy ingot is perforated and annealed at 700 ° C. 1 hour, and drawn into a thin tube with an outer diameter of Φ6mm and a wall thickness of 1mm. The copper-based alloy was annealed at 800°C for 1 hour and then directly drawn to Φ4mm. The two alloys were ultrasonically cleaned in alcohol, and then the gold alloy tube sleeve On the outer layer of the copper alloy rod, it is annealed at 700°C for 2 hours; it is forged by precision swaging, the deformation is controlled at about 25%, and then ...
PUM
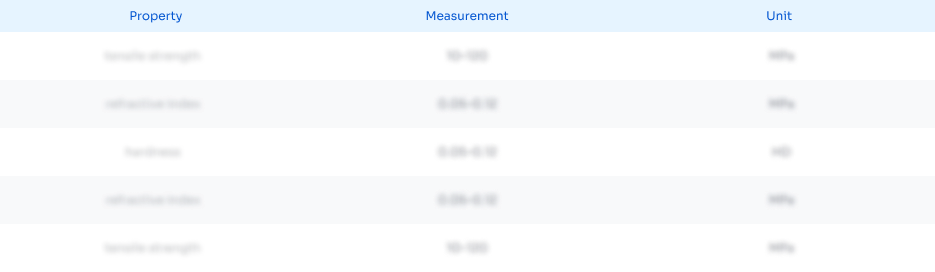
Abstract
Description
Claims
Application Information

- R&D Engineer
- R&D Manager
- IP Professional
- Industry Leading Data Capabilities
- Powerful AI technology
- Patent DNA Extraction
Browse by: Latest US Patents, China's latest patents, Technical Efficacy Thesaurus, Application Domain, Technology Topic, Popular Technical Reports.
© 2024 PatSnap. All rights reserved.Legal|Privacy policy|Modern Slavery Act Transparency Statement|Sitemap|About US| Contact US: help@patsnap.com