Cassava starch waste paper pulp composite foam material and preparation method thereof
A tapioca starch and composite foaming technology is applied in the field of environmental protection buffer packaging materials to achieve the effects of accelerating flow speed, increasing strength and promoting starch cross-linking
- Summary
- Abstract
- Description
- Claims
- Application Information
AI Technical Summary
Problems solved by technology
Method used
Image
Examples
Embodiment 1
[0016] (1) Treatment of waste paper pulp fibers: soak waste corrugated cardboard boxes in water for 24 hours at room temperature, then crush them, dry them in an oven at 110°C for 36 hours, and pass through a 100-mesh sieve to obtain waste paper pulp fibers;
[0017] (2) Raw materials: 600g of tapioca starch, 250g of waste paper pulp fiber, 150g of composite lubricant (1500 mesh calcium carbonate), 20% of the total amount of glycerin / urea composite plasticizer (90g of glycerol, 30g of urea);
[0018] (3) Soak waste paper pulp fibers in an aqueous solution of sodium hydroxide with a temperature of 30°C and a mass percentage of 5% for 15 minutes, wherein the mass ratio of waste paper pulp fibers to aqueous sodium hydroxide solution is 1:0.5;
[0019] (4) Dry 600g of tapioca starch in an oven at 60°C for 2 hours, and then blend it with the composite plasticizer in (2) above. Good 250g of waste paper pulp fiber, 150g of composite lubricant, at room temperature, blended for 15min; ...
Embodiment 2
[0024] (1) Treatment of waste paper pulp fibers: soak waste corrugated cardboard boxes in water for 48 hours at room temperature, then crush them, dry them in an oven at 100°C for 48 hours, and pass through a 150-mesh sieve to obtain waste paper pulp fibers;
[0025] (2) Raw materials: 750g of tapioca starch, 150g of waste paper pulp fiber, 100g of composite lubricant (1500 mesh calcium carbonate), 40% of the total amount of glycerin / urea composite plasticizer (glycerin 150g, urea 150g);
[0026] (3) Soak waste paper pulp fibers in an aqueous solution of sodium hydroxide with a temperature of 40°C and a mass percentage of 10% for 20 minutes, wherein the mass ratio of waste paper pulp fibers to aqueous sodium hydroxide solution is 1:1;
[0027] (4) Dry 750g of tapioca starch in an oven at 80°C for 3 hours, and then blend it with the composite plasticizer in (2) above. Good 150g waste paper pulp fiber, 100g compound lubricant, blending at room temperature for 20min;
[0028] (5...
Embodiment 3
[0032] (1) Treatment of waste paper pulp fibers: soak waste corrugated cardboard boxes in water for 36 hours at room temperature, dry them in an oven at 105°C for 36 hours, and then pulverize them, pass through a 120-mesh sieve to obtain waste paper pulp fibers;
[0033] (2) Raw materials: 700g of tapioca starch, 200g of waste paper pulp fiber, 100g of composite lubricant (1500 mesh calcium carbonate), 30% of the total amount of glycerin / urea composite plasticizer (glycerin 140g, urea 70g);
[0034] (3) Soak the waste paper pulp fibers in an aqueous solution of sodium hydroxide with a mass percentage of 8% at a temperature of 35°C for 20 minutes, wherein the mass ratio of the waste paper pulp fibers to the aqueous sodium hydroxide solution is 1:1;
[0035] (4) Dry 700g of tapioca starch in an oven at 70°C for 3 hours, and then blend it with the composite plasticizer in (2) above. Treated 200g of waste paper pulp fiber and 100g of composite lubricant were blended for 20min at r...
PUM
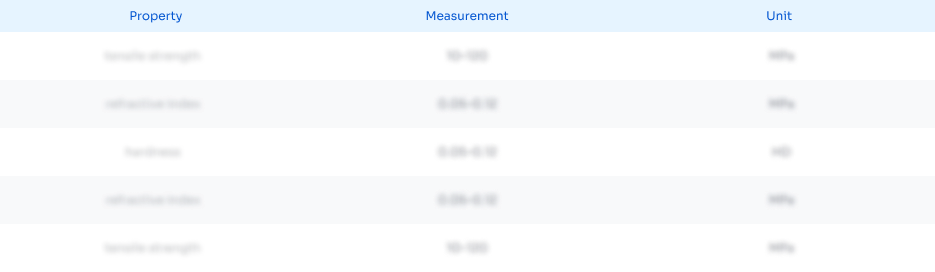
Abstract
Description
Claims
Application Information

- R&D Engineer
- R&D Manager
- IP Professional
- Industry Leading Data Capabilities
- Powerful AI technology
- Patent DNA Extraction
Browse by: Latest US Patents, China's latest patents, Technical Efficacy Thesaurus, Application Domain, Technology Topic, Popular Technical Reports.
© 2024 PatSnap. All rights reserved.Legal|Privacy policy|Modern Slavery Act Transparency Statement|Sitemap|About US| Contact US: help@patsnap.com