Calcination removal technology of carbon impurities in silicon carbide micro-powder
A technology of silicon carbide micropowder and carbon impurities, which is applied in the field of silicon carbide impurity removal, can solve the problems affecting the physical and chemical properties of SiC, and the application cannot reach the theoretical limit, etc., and achieve the effect of good carbon removal effect, low cost and easy operation
- Summary
- Abstract
- Description
- Claims
- Application Information
AI Technical Summary
Problems solved by technology
Method used
Examples
Embodiment 1
[0016] The calcination and removal process of carbon impurities in the silicon carbide micropowder of Example 1 includes the following steps:
[0017] S1: Load the silicon carbide micropowder into the magnetic boat, and use a tubular heat treatment furnace at 600 to 1200 ° C to keep calcined for 1 to 5 hours;
[0018] S2: cooling the product obtained from S1, pickling, and obtaining a solid product through multiple ultrasonic vibrations and centrifugation;
[0019] S3: drying the solid product in a drying oven to obtain the silicon carbide micropowder after removal of impurities.
[0020] Among them, the calcination temperature of the tubular heat treatment furnace in S1 is 900°C.
[0021] Among them, the heat preservation calcination time in S1 is 3h.
[0022] Wherein, the treatment solution of the pickling is a hydrochloric acid solution.
[0023] Wherein, the treatment liquid for ultrasonic vibration is a mixed liquid of water and acetone, and the weight percentage of wa...
Embodiment 2
[0025] The calcination and removal process of carbon impurities in the silicon carbide micropowder of embodiment 2 comprises the following steps:
[0026] S1: Load the silicon carbide micropowder into the magnetic boat, and use a tubular heat treatment furnace at 600 to 1200 ° C to keep calcined for 1 to 5 hours;
[0027] S2: cooling the product obtained from S1, pickling, and obtaining a solid product through multiple ultrasonic vibrations and centrifugation;
[0028] S3: drying the solid product in a drying oven to obtain the silicon carbide micropowder after removal of impurities.
[0029] Among them, the calcination temperature of the tubular heat treatment furnace in S1 is 925°C.
[0030] Among them, the heat preservation calcination time in S1 is 3.15h.
[0031] Wherein, the treatment solution of the pickling is a hydrochloric acid solution.
[0032] Wherein, the treatment liquid of ultrasonic vibration is a mixed liquid of water and acetone, and the weight percentage...
Embodiment 3
[0034] The calcination and removal process of carbon impurities in the silicon carbide micropowder of embodiment 3 comprises the following steps:
[0035] S1: Load the silicon carbide micropowder into the magnetic boat, and use a tubular heat treatment furnace at 600 to 1200 ° C to keep calcined for 1 to 5 hours;
[0036] S2: cooling the product obtained from S1, pickling, and obtaining a solid product through multiple ultrasonic vibrations and centrifugation;
[0037] S3: drying the solid product in a drying oven to obtain the silicon carbide micropowder after removal of impurities.
[0038] Among them, the calcination temperature of the tubular heat treatment furnace in S1 is 950°C.
[0039] Among them, the heat preservation calcination time in S1 is 3.3h.
[0040] Wherein, the treatment solution of the pickling is a hydrochloric acid solution.
[0041] Wherein, the treatment liquid of ultrasonic vibration is a mixed liquid of water and acetone, and the weight percentage ...
PUM
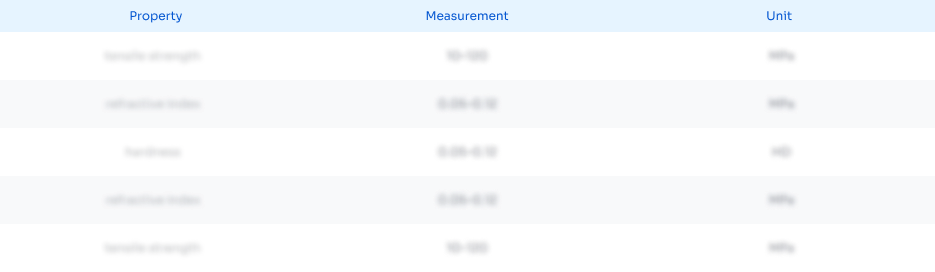
Abstract
Description
Claims
Application Information

- R&D
- Intellectual Property
- Life Sciences
- Materials
- Tech Scout
- Unparalleled Data Quality
- Higher Quality Content
- 60% Fewer Hallucinations
Browse by: Latest US Patents, China's latest patents, Technical Efficacy Thesaurus, Application Domain, Technology Topic, Popular Technical Reports.
© 2025 PatSnap. All rights reserved.Legal|Privacy policy|Modern Slavery Act Transparency Statement|Sitemap|About US| Contact US: help@patsnap.com