A self-adaptive control method for optical fiber winding tension
A technology of self-adaptive control and tension control, applied in the direction of self-adaptive control, general control system, control/adjustment system, etc., can solve the problem that cannot meet the requirements of fast follow-up, control accuracy and winding speed of the fiber take-up shaft and the high-precision winding of the fiber supply shaft It is very high, affecting the tension control accuracy, etc., to achieve the effect of improving the tension control accuracy, fast tracking speed, and good speed smoothness.
- Summary
- Abstract
- Description
- Claims
- Application Information
AI Technical Summary
Problems solved by technology
Method used
Image
Examples
Embodiment Construction
[0024] The present invention will be further described in detail below in conjunction with the accompanying drawings and specific embodiments.
[0025] The self-adaptive control method for optical fiber winding tension of the present invention is based on speed dynamic programming and trajectory subdivision technology, please refer to figure 1 As shown, it mainly includes the following steps:
[0026] (1) Establish a dynamic adaptive model of the tension control system based on the dynamic compensation of the winding radius of the fiber winding machine: see figure 2 As shown, the tension control system in the present invention is made up of fiber receiving shaft 201, first fiber guide wheel 202, tension sensor 203, tension wheel 204, second fiber guide wheel 2205, fiber supply shaft 206 and rotation axis 207; the present invention The structure of the tension control system adopts the structure that the fiber receiving shaft 201 actively collects the fiber, and the fiber sup...
PUM
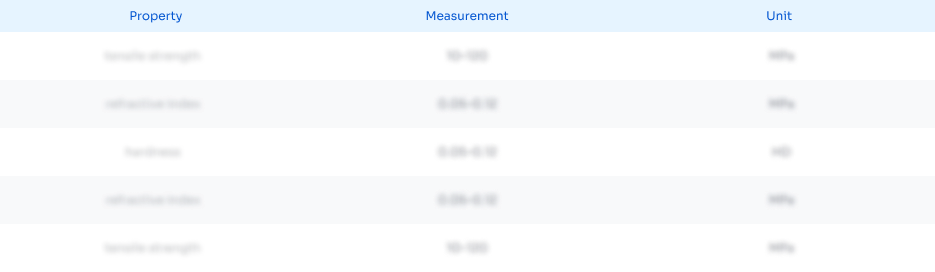
Abstract
Description
Claims
Application Information

- R&D
- Intellectual Property
- Life Sciences
- Materials
- Tech Scout
- Unparalleled Data Quality
- Higher Quality Content
- 60% Fewer Hallucinations
Browse by: Latest US Patents, China's latest patents, Technical Efficacy Thesaurus, Application Domain, Technology Topic, Popular Technical Reports.
© 2025 PatSnap. All rights reserved.Legal|Privacy policy|Modern Slavery Act Transparency Statement|Sitemap|About US| Contact US: help@patsnap.com