Preparation method of high-hydrophobicity polyvinylidene fluoride hollow fiber membrane
A polyvinylidene fluoride, high hydrophobic technology, applied in chemical instruments and methods, membranes, membrane technology, etc., can solve the problems of low porosity, can not meet high flux, etc., to improve hydrophobicity, improve anti-wetting ability, the effect of improving mechanical strength
- Summary
- Abstract
- Description
- Claims
- Application Information
AI Technical Summary
Problems solved by technology
Method used
Image
Examples
Embodiment 1
[0031] Preparation of PVDF casting solution: place 0.5g of nano-silica and 3g of polyvinylpyrrolidone (K30) in 84.5g of N,N-dimethylformamide (DMF) in proportion, first ultrasonically disperse for 2 hours, and then continue at a constant speed Stir mechanically for 10 hours to obtain a base solution, dissolve 13 g of PVDF in the base solution, heat in a constant temperature water bath at 50°C, and stir mechanically for 10 hours to obtain a casting solution.
[0032] PVDF hollow fiber membrane spinning process: place the prepared casting liquid in the slurry tank of the spinning machine, vacuum remove the residual air in the casting liquid at a constant temperature of 50°C, and then let it stand for 12 hours to remove the casting film Air bubbles in the liquid, a hollow fiber liner is installed in the spinneret of the spinning machine, the extrusion rate of the cast film liquid is adjusted to 4mL / min, the extrusion rate of the liner is 1m / min, the air distance is adjusted to 10c...
Embodiment 2
[0036]Preparation of PVDF casting solution: place 1g of nano-silica and 4g of polyvinylpyrrolidone (K30) in 82g of N,N-dimethylformamide (DMF), ultrasonically disperse for 3 hours, and then continue to stir mechanically at a uniform speed After 12 hours, the base solution was obtained, and 14 g of PVDF was dissolved in the base solution, heated in a constant temperature water bath at 60° C., and mechanically stirred for 12 hours to obtain a casting solution.
[0037] PVDF hollow fiber membrane spinning process: place the prepared casting liquid in the slurry tank of the spinning machine, vacuum remove the residual air in the casting liquid at a constant temperature of 60°C, and then let it stand for 16 hours to remove the casting film bubbles in the liquid. Install a hollow fiber liner in the spinneret of the spinning machine, adjust the extrusion rate of the casting liquid to 6mL / min, the extrusion rate of the liner to 2m / min, and adjust the air gap to 10cm to carry out spinn...
Embodiment 3
[0041] Preparation of PVDF casting solution: put 1.5g of nano-titanium dioxide and 5g of polyethylene glycol-400 (PEG400) in 79.5g of N,N-dimethylacetamide (DMAC), ultrasonically disperse for 4 hours, and then continue at a constant speed Stir mechanically for 14 hours to obtain a base solution, dissolve 15 g of PVDF in the base solution, heat in a constant temperature water bath at 70°C, and stir mechanically for 14 hours to obtain a casting solution.
[0042] PVDF hollow fiber membrane spinning process: place the prepared casting solution in the slurry tank of the spinning machine, vacuum remove the residual air in the casting solution at a constant temperature of 70°C, and then let it stand for 24 hours to remove the casting film bubbles in the liquid. Install the hollow fiber liner in the spinneret of the spinning machine, adjust the extrusion rate of casting liquid to 8mL / min, the extrusion rate of the liner to 3m / min, and adjust the air distance to 15cm to carry out spin...
PUM
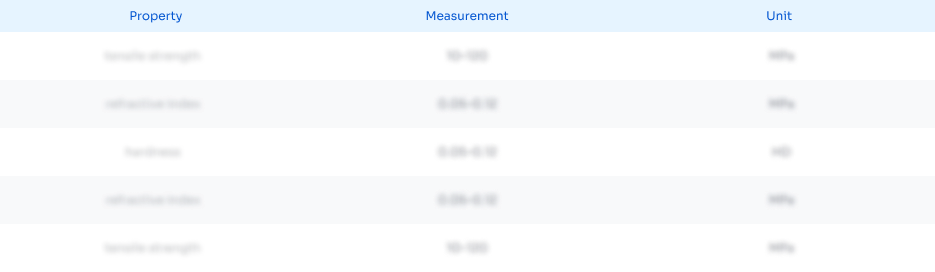
Abstract
Description
Claims
Application Information

- R&D
- Intellectual Property
- Life Sciences
- Materials
- Tech Scout
- Unparalleled Data Quality
- Higher Quality Content
- 60% Fewer Hallucinations
Browse by: Latest US Patents, China's latest patents, Technical Efficacy Thesaurus, Application Domain, Technology Topic, Popular Technical Reports.
© 2025 PatSnap. All rights reserved.Legal|Privacy policy|Modern Slavery Act Transparency Statement|Sitemap|About US| Contact US: help@patsnap.com