Quad redundant angular displacement sensor
An angular displacement sensor and four-redundancy technology, applied in instruments, measuring devices, electrical devices, etc., can solve the problems of large size, limited use occasions, inconvenient installation and adjustment, etc.
- Summary
- Abstract
- Description
- Claims
- Application Information
AI Technical Summary
Problems solved by technology
Method used
Image
Examples
Embodiment Construction
[0012] The present invention will be described in further detail below in conjunction with accompanying drawing and embodiment:
[0013] See attached Figure 1~3 As shown, this four-degree redundant angular displacement sensor is characterized in that: the sensor includes four identical angular displacement sensor assemblies (1), and each angular position of a four-degree redundant angular displacement sensor displacement sensor assembly (1) includes An angular displacement sensor (9) and a gear (10) connected to the output shaft of the angular displacement sensor (9) and an anti-backlash gear (11) matched together with the gear (10);
[0014] The sensor also includes a hollow U-shaped housing (2), the U-shaped housing (2) and the cover plate (3) are connected together by four screws to form the supporting structure of the entire sensor, and the gear shaft (4) passes through the shaft The bearing (5) and the shaft end bearing (7) are installed on the U-shaped housing (2) and ...
PUM
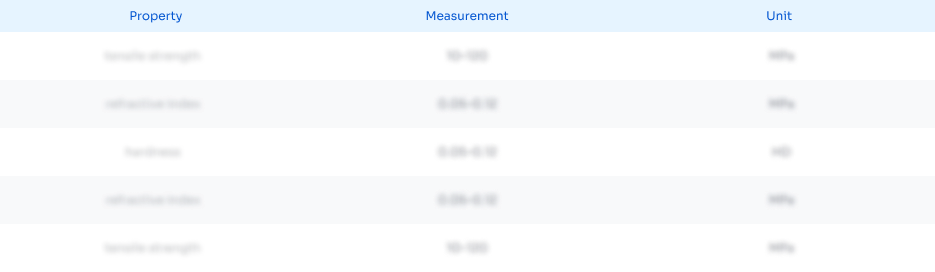
Abstract
Description
Claims
Application Information

- Generate Ideas
- Intellectual Property
- Life Sciences
- Materials
- Tech Scout
- Unparalleled Data Quality
- Higher Quality Content
- 60% Fewer Hallucinations
Browse by: Latest US Patents, China's latest patents, Technical Efficacy Thesaurus, Application Domain, Technology Topic, Popular Technical Reports.
© 2025 PatSnap. All rights reserved.Legal|Privacy policy|Modern Slavery Act Transparency Statement|Sitemap|About US| Contact US: help@patsnap.com