Preparation method of polyhexamethyleneguanidine hydrochloride
A technology of polyhexamethylene guanidine hydrochloride and guanidine hydrochloride, which is applied in the field of polymer preparation, can solve problems such as product quality impact, and achieve the effects of simplifying production process, improving product yield and being convenient to use.
- Summary
- Abstract
- Description
- Claims
- Application Information
AI Technical Summary
Problems solved by technology
Method used
Examples
Embodiment 1
[0034] Put the raw materials 1,6-hexamethylenediamine and guanidine hydrochloride into a three-necked flask, wherein the molar ratio of 1,6-hexamethylenediamine and guanidine hydrochloride is 1.05:1, raise the temperature of the material to 140°C for 6 hours, then raise the temperature to 190°C and then Reaction 2h. Cool the material, lower the material temperature to 150°C, add 15% sodium hydroxide solution in an equimolar ratio to 1,6-hexanediamine, and keep the temperature at 100°C for 2 hours. The aqueous solution of the lower layer was separated, and the upper layer of polyhexamethyleneguanidine was rinsed twice with deionized water. Dissolve the rinsed polyhexamethyleneguanidine with 15% hydrochloric acid, adjust the pH of the polyhexamethyleneguanidine hydrochloride solution to 6.5, and vacuum-dry the solution at 120°C to obtain a solid polyhexamethyleneguanidine hydrochloride product. The product has a purity of 96.7%, a yield of 92.3%, Mn=1105.9, Mw=1198.3.
Embodiment 2
[0036]Put the raw materials 1,6-hexamethylenediamine and guanidine hydrochloride into a three-neck flask, wherein the molar ratio of 1,6-hexamethylenediamine and guanidine hydrochloride is 1.05:1, raise the temperature of the material to 150°C for 5 hours, then raise the temperature to 185°C Reaction 3h. Cool the material, lower the material temperature to 150°C, add 15% sodium hydroxide solution in an equimolar ratio to 1,6-hexanediamine, and keep the temperature at 105°C for 2 hours. The aqueous solution of the lower layer was separated, and the upper layer of polyhexamethyleneguanidine was rinsed twice with deionized water. The rinsed polyhexamethyleneguanidine was dissolved with 15% hydrochloric acid, the pH of the polyhexamethyleneguanidine hydrochloride solution was adjusted to 6.5, and the solution was vacuum-dried at 120°C to obtain a solid polyhexamethyleneguanidine hydrochloride product. The product has a purity of 97.2%, a yield of 93.5%, Mn=1015.4, Mw=1156.7.
Embodiment 3
[0038] Put the raw materials 1,6-hexamethylenediamine and guanidine hydrochloride into a three-necked flask, wherein the molar ratio of 1,6-hexamethylenediamine and guanidine hydrochloride is 1.10:1, raise the temperature of the material to 140°C for 8 hours, then raise the temperature to 185°C Reaction 3h. Cool the material, lower the material temperature to 150°C, add 10% sodium hydroxide solution in an equimolar ratio to 1,6-hexanediamine, and keep the temperature at 100°C for 2 hours. The aqueous solution of the lower layer was separated, and the upper layer of polyhexamethyleneguanidine was rinsed twice with deionized water. The rinsed polyhexamethyleneguanidine was dissolved with 15% hydrochloric acid, the pH of the polyhexamethyleneguanidine hydrochloride solution was adjusted to 6.5, and the solution was vacuum-dried at 120°C to obtain a solid polyhexamethyleneguanidine hydrochloride product. Product purity 97.4%, yield 91.8%, Mn=997.3, Mw=1147.2.
PUM
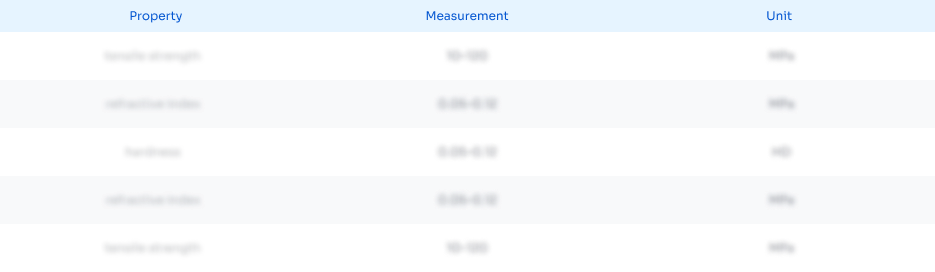
Abstract
Description
Claims
Application Information

- R&D Engineer
- R&D Manager
- IP Professional
- Industry Leading Data Capabilities
- Powerful AI technology
- Patent DNA Extraction
Browse by: Latest US Patents, China's latest patents, Technical Efficacy Thesaurus, Application Domain, Technology Topic, Popular Technical Reports.
© 2024 PatSnap. All rights reserved.Legal|Privacy policy|Modern Slavery Act Transparency Statement|Sitemap|About US| Contact US: help@patsnap.com