Laminated material and method for making the same
A technology of laminated material and surface layer, applied in chemical instruments and methods, layered products, synthetic resin layered products, etc., can solve the problems of complicated processing process, unnecessary cost increase, poor adhesion effect, etc.
- Summary
- Abstract
- Description
- Claims
- Application Information
AI Technical Summary
Problems solved by technology
Method used
Image
Examples
Embodiment Construction
[0024] refer to Figure 1 to Figure 6 , which shows a schematic diagram of the process steps of the manufacturing method of the first embodiment of the laminated material of the present invention. refer to figure 1 , a release paper 10 is provided. The release paper 10 has a first surface 101 . Preferably, the release paper 10 has a release pattern on the first surface 101 .
[0025] refer to figure 2 , forming a second polymer mixture on the first surface 101 of the release paper 10 by coating, wherein the second polymer mixture includes a second polymer resin. The solid content of the second polymer resin is 15% to 60% by weight, the viscosity is 500 to 10000cps, the preferred solid content is 25 to 35% by weight, and the preferred viscosity is 700 to 2500cps, and the second polymer resin The material of the resin is polyurethane resin, water-soluble elastomer resin or water-dispersed elastomer resin. Then, the second polymer mixture is gradually dried at a temperatur...
PUM
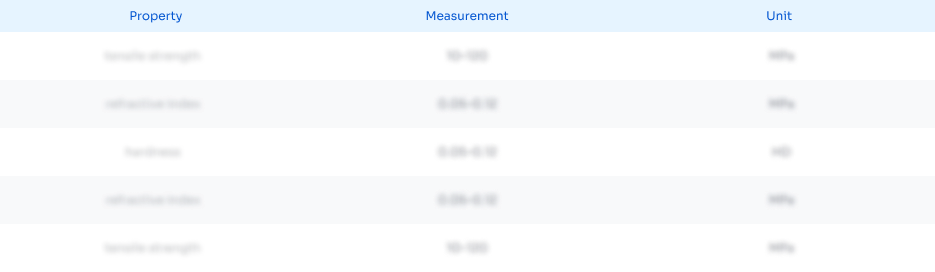
Abstract
Description
Claims
Application Information

- R&D Engineer
- R&D Manager
- IP Professional
- Industry Leading Data Capabilities
- Powerful AI technology
- Patent DNA Extraction
Browse by: Latest US Patents, China's latest patents, Technical Efficacy Thesaurus, Application Domain, Technology Topic, Popular Technical Reports.
© 2024 PatSnap. All rights reserved.Legal|Privacy policy|Modern Slavery Act Transparency Statement|Sitemap|About US| Contact US: help@patsnap.com