A three-media braided wire mesh material heat exchanger and its manufacturing method
The technology of a metal wire mesh and a manufacturing method is applied in the direction of heat exchanger type, indirect heat exchanger, heat transfer modification, etc., and can solve the problems of complex manufacturing process, large residual stress of metal mesh core, poor bearing capacity, etc. To achieve the effect of ensuring heat exchange efficiency, improving the scope of use, and improving service life
- Summary
- Abstract
- Description
- Claims
- Application Information
AI Technical Summary
Problems solved by technology
Method used
Image
Examples
Embodiment Construction
[0051] Figure 1~10 It is the best embodiment of the present invention, below in conjunction with attached Figure 1~10 The present invention will be further described.
[0052] A three-media braided wire mesh material heat exchanger, including a compression plate 1, a guide rod and a connecting pipe 3, and a multi-piece metal mesh heat exchange unit is arranged between the two compression plates 1, and the multi-piece metal mesh heat exchange unit The units are superimposed and fixed by the guide rod and the pressing plate 1;
[0053] The metal mesh heat exchange unit includes a heat exchange plate 7, sealing plates 6 on both sides of the heat exchange plate 7, and a metal mesh core 11. A heat exchange cavity 9 is provided in the middle of the heat exchange plate 7, and the metal mesh core 11 is arranged on the heat exchange plate. In the cavity 9, it is sealed by the sealing plates 6 on both sides;
[0054] The heat exchange chamber 9 of the metal mesh heat exchange unit ...
PUM
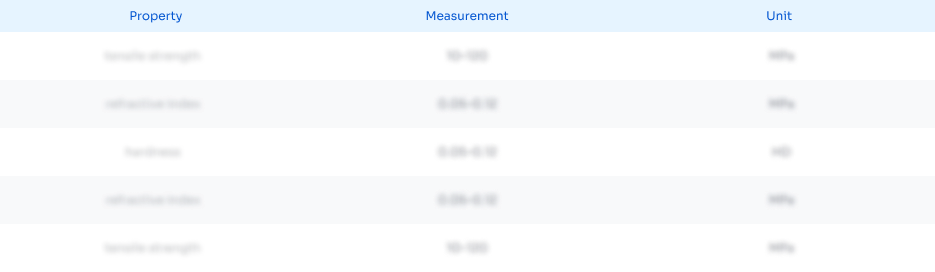
Abstract
Description
Claims
Application Information

- R&D Engineer
- R&D Manager
- IP Professional
- Industry Leading Data Capabilities
- Powerful AI technology
- Patent DNA Extraction
Browse by: Latest US Patents, China's latest patents, Technical Efficacy Thesaurus, Application Domain, Technology Topic, Popular Technical Reports.
© 2024 PatSnap. All rights reserved.Legal|Privacy policy|Modern Slavery Act Transparency Statement|Sitemap|About US| Contact US: help@patsnap.com