Automatic finish machining method for cambered thick plate groove in suspended state
A curved surface and bevel technology, which is applied in the field of automatic finishing of curved surface thick plate bevels in the suspended state, can solve problems such as difficult quality control, engineering quality and later production safety impact, and high risk of high-altitude operations, so as to improve cutting efficiency, The effect of shortening the rapid overhaul time and avoiding the risk of working at heights
- Summary
- Abstract
- Description
- Claims
- Application Information
AI Technical Summary
Problems solved by technology
Method used
Image
Examples
Embodiment Construction
[0017] Such as figure 1 As shown, a method for automatic finishing of curved surface thick plate grooves in a suspended state, which includes the following procedures:
[0018] (1) Erect the operating platform along the curved surface;
[0019] (2) A walking device is provided; the walking device can walk around the curved surface through the operating platform;
[0020] (3) Adjust the positioning of the walking device;
[0021] (4) Set the guide mechanism and adjust the angle positioning so that the cutting nozzle is aligned with the cutting line;
[0022] (5) Carry out trial cutting and fine-tune the cutting nozzle;
[0023] (6) Formal cutting to form a bevel.
PUM
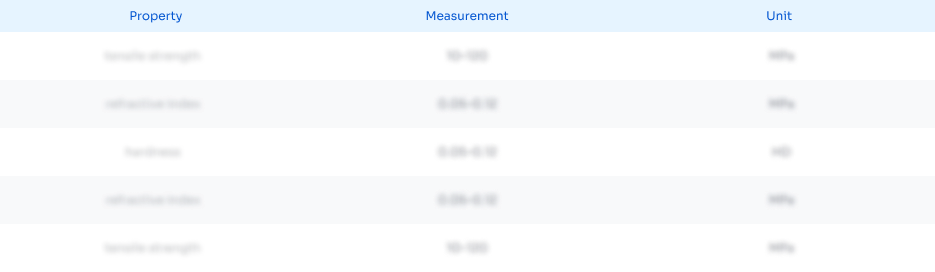
Abstract
Description
Claims
Application Information

- R&D Engineer
- R&D Manager
- IP Professional
- Industry Leading Data Capabilities
- Powerful AI technology
- Patent DNA Extraction
Browse by: Latest US Patents, China's latest patents, Technical Efficacy Thesaurus, Application Domain, Technology Topic, Popular Technical Reports.
© 2024 PatSnap. All rights reserved.Legal|Privacy policy|Modern Slavery Act Transparency Statement|Sitemap|About US| Contact US: help@patsnap.com