Method of recycling polyphenylene sulfide and PTFE waste filter materials
A polytetrafluoroethylene and polyphenylene sulfide technology is applied in the field of recycling polyphenylene sulfide and polytetrafluoroethylene waste and old filter materials, which can solve the problems of high price of dust removal bags, high unit price, and limited application of dust removal bags. Achieving the effect of good shape following and high elongation at break
- Summary
- Abstract
- Description
- Claims
- Application Information
AI Technical Summary
Problems solved by technology
Method used
Examples
Embodiment 1
[0032] Collect the waste filter material of polyphenylene sulfide and polytetrafluoroethylene→cleaning→drying→segmentation to obtain a block filter material with a rule of about 300mm, weigh 22.3g of it and melt it at 330℃, and fully Stir for 4h, add 3.2g glass fiber, 1g carbon fiber, 0.5g SiC, 1.1g MoS in sequence 2 , 0.6g of hollow glass beads, 0.2g of coal ash, 0.2g of carbon particles and 0.3g of graphite particles, supplemented with 4.1g of PTFE, continue to stir for 2h, and finally pass the melt through the extrusion device to make the corresponding product .
[0033] The products obtained above were subjected to impact performance test according to ISO180-93, tensile performance test according to ISO527-93, and bending performance test according to ISO178-93. The test results are shown in Table 1.
Embodiment 2
[0035] Collect the waste filter material of polyphenylene sulfide and polytetrafluoroethylene→cleaning→drying→segmentation to obtain a block filter material with a rule of about 300mm. Weigh 17.6g of it and melt it at 340℃, and fully Stir for 3h, add 1.7g glass fiber, 1g carbon fiber, 0.4g SiC, 1.0g MoS in sequence 2 , 0.4g hollow glass beads, 0.2g coal ash, 0.2g carbon particles and 0.3g graphite particles, supplemented with 3.4g PTFE, continue to stir for 2h, and finally the melt is passed through the extrusion device to make the corresponding product .
[0036] The product obtained above was tested for mechanical properties according to the test method of Example 1, and compared with common PTFE products on the market. The test results are shown in Table 1.
Embodiment 3
[0038] Collect the waste filter material of polyphenylene sulfide and polytetrafluoroethylene→cleaning→drying→segmentation to obtain a block filter material with a rule of about 300mm, weigh 18.2g of it and melt it at 350℃, and fully Stir for 3h, add 1.9g glass fiber, 1.1g carbon fiber, 0.5g SiC, 1.1g MoS in sequence 2 , 0.4g hollow glass beads, 0.3g coal ash, 0.3g carbon particles and 0.2g graphite particles, supplemented with 3.7g PTFE, continue to stir for 2h, and finally the melt is passed through the extrusion device to make the corresponding product .
[0039] The product obtained above was subjected to mechanical performance test according to the test method of Example 1, and the test results are shown in Table 1.
[0040] Table 1 Test results of mechanical properties of the product of the present invention
[0041] Category
[0042] It has been tested that the product of the present invention has stable performance. Compared with normal PTFE products, the mechanical perfo...
PUM
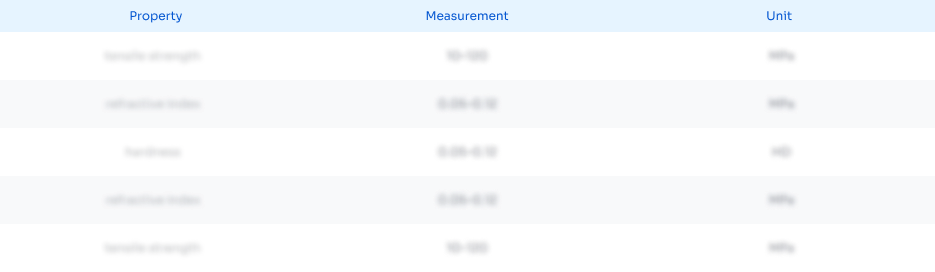
Abstract
Description
Claims
Application Information

- R&D
- Intellectual Property
- Life Sciences
- Materials
- Tech Scout
- Unparalleled Data Quality
- Higher Quality Content
- 60% Fewer Hallucinations
Browse by: Latest US Patents, China's latest patents, Technical Efficacy Thesaurus, Application Domain, Technology Topic, Popular Technical Reports.
© 2025 PatSnap. All rights reserved.Legal|Privacy policy|Modern Slavery Act Transparency Statement|Sitemap|About US| Contact US: help@patsnap.com