Pumping unit brake structure with heat radiating function
A pumping unit, functional technology, applied in the direction of brake actuators, gear transmission mechanisms, mechanical equipment, etc., can solve the problem of not being able to ensure that the beam pumping unit stops working quickly, the pumping unit cannot stop working quickly, and bad chain Response and other problems, to achieve the effect of small footprint, high temperature reduction, reduced life expectancy
- Summary
- Abstract
- Description
- Claims
- Application Information
AI Technical Summary
Problems solved by technology
Method used
Image
Examples
specific Embodiment 1
[0027] Specific embodiment one, see Figure 1 ~ Figure 3 : The linear feed part 6 is an oil cylinder structure, the output part 7 is a piston rod, the position of the brake pad support 5 facing the brake disc 4 is fastened with an oil cylinder structure, the piston rod of the oil cylinder structure is arranged towards the outer end surface of the brake disc 4, and the piston A brake pad 8 is fastened on the rod, and the braking area of the brake pad 8 is arranged toward the outer end surface of the brake disc 4, and an oil pump structure 18 is externally connected to the cavity of the oil cylinder structure through an oil pipe 17;
specific Embodiment 2
[0028] Specific embodiment two: the linear feed part 6 is an electric cylinder structure, and the position of the brake pad support 5 towards the brake disc 4 is fastened with an electric cylinder structure, and the piston rod of the electric cylinder structure is arranged towards the outer end surface of the brake disc 4. The piston rod of the cylinder structure is fastened with a brake pad 8, the braking surface of the brake pad 8 is arranged towards the outer end surface of the brake disc 4, and the electric cylinder is connected to an external power supply through a wire;
specific Embodiment 3
[0029] Specific embodiment three: the linear feed component 6 is a cylinder structure, the position of the brake pad support 5 towards the brake disc 4 is fastened with a cylinder structure, the piston rod of the cylinder structure is arranged towards the outer end surface of the brake disc 4, and the piston of the cylinder structure A brake pad 8 is fastened on the rod, and the braking area of the brake pad 8 is arranged toward the outer end surface of the brake disc 4, and a compressed air source is externally connected to the cavity of the cylinder structure through a gas pipe.
PUM
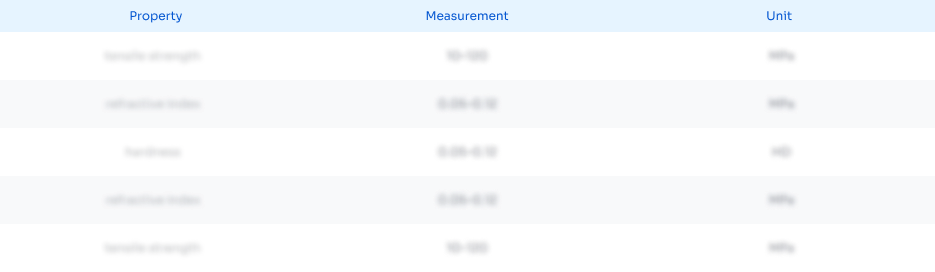
Abstract
Description
Claims
Application Information

- R&D Engineer
- R&D Manager
- IP Professional
- Industry Leading Data Capabilities
- Powerful AI technology
- Patent DNA Extraction
Browse by: Latest US Patents, China's latest patents, Technical Efficacy Thesaurus, Application Domain, Technology Topic, Popular Technical Reports.
© 2024 PatSnap. All rights reserved.Legal|Privacy policy|Modern Slavery Act Transparency Statement|Sitemap|About US| Contact US: help@patsnap.com