Rubber asphalt and preparation method thereof
A technology of rubber asphalt and rubber, which is applied in the field of rubber asphalt and its preparation, can solve the problems of re-aging of active groups, affecting the service life of the road surface, and long production cycle, and achieve chemical stability of the colloid system, enhanced workability, and good compatibility effect
- Summary
- Abstract
- Description
- Claims
- Application Information
AI Technical Summary
Problems solved by technology
Method used
Image
Examples
Embodiment 1
[0056] Heat the mixture of No. 30 straight-run asphalt with 78.4% of the total mass of rubber asphalt and No. 90 blended asphalt (weight ratio 3:7) to 120°C on a heating mantle, and add 80 mesh waste with 21% of the total mass of rubber asphalt while stirring. Tire rubber powder and 0.1% n-dodecanethiol were stirred at a speed of 1300 rpm for 5 minutes to form a uniformly mixed mixture. When the temperature rises to 180°C, use a high-shear dispersing emulsifier for high-speed shearing and stirring for 15 minutes. During the shearing process, the temperature is controlled at (180±3)°C, and the speed is 3000 rpm, and then the total mass of rubber asphalt is added. 0.5% mixture of 6-ethoxy-2,2,4-trimethyl-1,2-dihydroquinoline and 3-hydroxybutyraldehyde-α-naphthylamine (ratio 1:1) with a stirrer Stirring, the temperature is controlled at (180±3)°C during the stirring reaction process, and the stirring time is 3 hours to obtain the finished rubber asphalt.
Embodiment 2
[0058] Heat No. 70 blended asphalt with 75% of the total mass of rubber asphalt to 130°C on a heating mantle, add 60 mesh waste tire rubber powder with 24% of the total mass of rubber asphalt and 0.5% rubber activator 480 while stirring, and the speed is 1300 rpm and stir for 10 minutes to form a well-mixed mixture. When the temperature rises to 180°C, use a high-shear dispersing emulsifier for high-speed shearing and stirring for 10 minutes. During the shearing process, the temperature is controlled at (180±3)°C, and the speed is 4000 rpm, and then the total mass of rubber asphalt is added. The mixture of 0.5% acetaldehyde-α-naphthalene condensate and N-phenyl-α-naphthylamine (ratio 1:1) is stirred with a stirrer, and the temperature is controlled at (180±3)°C during the stirring reaction, and the stirring The time is 3 hours, and the rubber asphalt finished product is obtained.
Embodiment 3
[0060] Heat No. 50 oxidized asphalt with 75.5% of the total mass of rubber asphalt to 150°C on a heating mantle, and add 60 mesh waste tire rubber powder with 23% of the total mass of rubber asphalt and 0.5% of xylene disulfide and phenol disulfide while stirring. The mixture of sulfides (ratio 1:1) was stirred at 1000 rpm for 10 minutes to form a well-mixed mixture. When the temperature rises to 180°C, use a high-shear dispersing emulsifier for high-speed shearing and stirring for 15 minutes. During the shearing process, the temperature is controlled at (180±3)°C, and the speed is 3000 rpm, and then the total mass of rubber asphalt is added. The mixture (ratio 1:1) of 1% acetaldehyde-α naphthalene condensate' and N-phenyl-β-naphthylamine is stirred with a stirrer, and the temperature is controlled at (180±3)°C during the stirring reaction, The stirring time is 2 hours, and the rubber asphalt product is obtained.
PUM
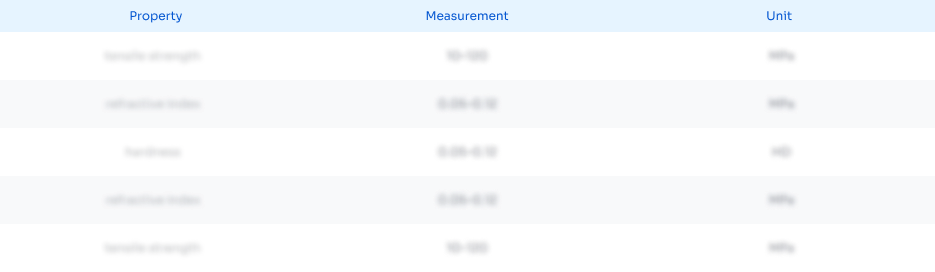
Abstract
Description
Claims
Application Information

- R&D
- Intellectual Property
- Life Sciences
- Materials
- Tech Scout
- Unparalleled Data Quality
- Higher Quality Content
- 60% Fewer Hallucinations
Browse by: Latest US Patents, China's latest patents, Technical Efficacy Thesaurus, Application Domain, Technology Topic, Popular Technical Reports.
© 2025 PatSnap. All rights reserved.Legal|Privacy policy|Modern Slavery Act Transparency Statement|Sitemap|About US| Contact US: help@patsnap.com