Method for preparing oil-based composite oil product drag reducer from finished oil decoloring spent bleaching clay
A technology of waste clay and drag reducer, which is applied in the field of drag reduction and increase transmission, can solve the problems of drag reducer loss of application performance, molecular chain breakage and shear degradation, etc., to reduce the cost of injection application, promote synergy, and enhance application performance effect
- Summary
- Abstract
- Description
- Claims
- Application Information
AI Technical Summary
Problems solved by technology
Method used
Image
Examples
Embodiment 1
[0028] Embodiment 1: The method for preparing an oil-based composite oil drag reducer from the decolorized waste clay of finished oil mentioned in the present invention is as follows:
[0029] Weigh 100g of waste clay after gasoline decolorization, put it into a ball mill for grinding for 60min, sieve through a 400-mesh sieve, keep the waste clay powder that has passed through the sieve, dry it at 100°C for 48h, and then place it in a muffle furnace. Under the protection of nitrogen, bake at 600°C for 4h;
[0030] Weigh 5g of roasted waste clay, add 50g of deionized water, and stir for 60min at 30°C and 200r / min; then weigh 10g of titanate KR-9S and slowly add it to the beaker, and continue at 30°C, ultrasonically Treat for 60 minutes; at this time, add 1g of cetyltrimethylammonium bromide, control the temperature at 40°C, and stir at 80r / min for 60min until the mixture is complete; then add 0.05g of dodecyl betaine, 40°C and 50r / min, stirring for 60min until the mixture is c...
Embodiment 2
[0033] Embodiment 2: The method for preparing an oil-based composite oil product drag reducer from the refined oil decolorization waste clay mentioned in the present invention is as follows:
[0034] Weigh 100g of waste clay after decolorization of alkylated oil, put it into a ball mill for grinding for 20 minutes, and sieve through a 400-mesh sieve, keep the waste clay powder that has passed through the screen, dry it at 80°C for 24 hours, and then place it in a muffle In the furnace, under the protection of nitrogen, bake at 400 °C for 1 h.
[0035] Weigh 5g of roasted waste clay, add 25g of deionized water, and stir at 20°C and 100r / min for 30min; then weigh 5g of titanate KR-9S and slowly add it to the beaker, and continue at 20°C, ultrasonically Treat for 30 minutes; at this time, add 0.5g cetyltrimethylammonium bromide, control the temperature at 20°C, and stir at 50r / min for 30min; then add 0.1g dodecyl betaine, 30°C and 50r / min min, stirring for 10 min.
[0036]Throu...
Embodiment 3
[0037] Embodiment 3: The method for preparing an oil-based composite oil drag reducer from the waste clay for decolorizing finished oil mentioned in the present invention is as follows:
[0038] Weigh 100g of waste clay after decolorization of diesel oil, put it into a ball mill for grinding for 40min, sieve through a 400-mesh sieve, keep the waste clay powder that has passed through the sieve, dry it at 90°C for 36h, and then place it in a muffle furnace. Under the protection of nitrogen, calcined at 400°C for 3h.
[0039] Weigh 5g of roasted waste clay, add 40g of deionized water, and stir for 45min at 25°C and 150r / min; then weigh 8g of titanate KR-9S and slowly add it to the beaker, and continue at 25°C, ultrasonically Treat for 50 minutes; at this time, add 0.8g of dodecyltrimethylammonium bromide, control the temperature at 30°C, and stir at 70r / min for 50min; then add 0.08g of dodecyldiethanolamide, 35°C and 50r / min, stirring for 40min.
[0040] According to the dies...
PUM
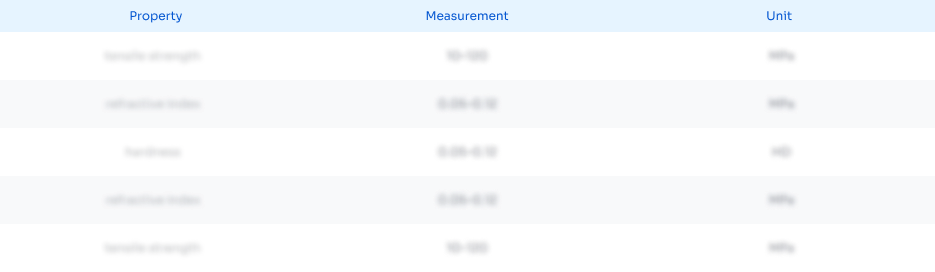
Abstract
Description
Claims
Application Information

- Generate Ideas
- Intellectual Property
- Life Sciences
- Materials
- Tech Scout
- Unparalleled Data Quality
- Higher Quality Content
- 60% Fewer Hallucinations
Browse by: Latest US Patents, China's latest patents, Technical Efficacy Thesaurus, Application Domain, Technology Topic, Popular Technical Reports.
© 2025 PatSnap. All rights reserved.Legal|Privacy policy|Modern Slavery Act Transparency Statement|Sitemap|About US| Contact US: help@patsnap.com