System for preparing methyl alcohol with coke oven gas and method for preparing methyl alcohol through system
A technology of coke oven gas and coke oven, which is applied in the field of coal chemical industry, can solve the problems of low space velocity, high difficulty, and inability to circulate nitrogen, and achieve the effect of slow temperature rise and long driving time
- Summary
- Abstract
- Description
- Claims
- Application Information
AI Technical Summary
Problems solved by technology
Method used
Image
Examples
Embodiment 1
[0056] Such as image 3 As shown, the system for preparing methanol with coke oven gas includes a fine desulfurization system and a conversion system; the fine desulfurization system includes a first coke oven gas compressor, a first heating furnace and a fine desulfurization section connected by pipelines in sequence; The reforming system includes a second coke oven gas compressor, a second heating furnace and a reforming section connected in sequence by pipelines;
[0057] The first coke oven gas compressor is used to provide coke oven gas to the fine desulfurization system;
[0058] The first heating furnace receives the coke oven gas from the first coke oven gas compressor to heat it;
[0059] The fine desulfurization section receives coke oven gas from the first heating furnace;
[0060] The second coke oven gas compressor is used to provide nitrogen to the reforming system;
[0061] The second heating furnace receives nitrogen from the second coke oven gas compressor ...
Embodiment 2
[0079] Such as Figure 5 Shown, the system that prepares methanol with coke oven gas, in embodiment 1 image 3 On the basis of the system shown, there is also a fine desulfurization main auxiliary line, one end of the fine desulfurization main auxiliary line is arranged on the pipeline from the first heating furnace to the fine desulfurization section, and the other end is arranged on the pipeline from the first heating furnace to the fine desulfurization section. The first valve is connected to the pipeline of the conversion system.
[0080] Figure 5 The system shown in Example 1 is image 3 The heating process of the system shown is consistent. because Figure 5 is in figure 1 shown on the basis of the existing design, while the figure 1 The existing design shown includes the main auxiliary line of fine desulfurization, and the pipeline of the main auxiliary line of fine desulfurization is not easy to remove. Therefore, in order to simplify the operation steps when im...
PUM
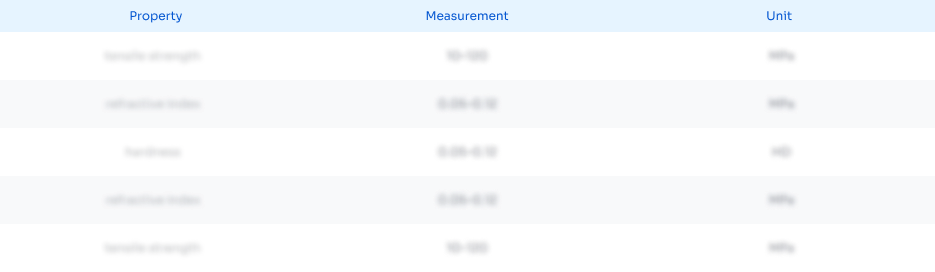
Abstract
Description
Claims
Application Information

- R&D
- Intellectual Property
- Life Sciences
- Materials
- Tech Scout
- Unparalleled Data Quality
- Higher Quality Content
- 60% Fewer Hallucinations
Browse by: Latest US Patents, China's latest patents, Technical Efficacy Thesaurus, Application Domain, Technology Topic, Popular Technical Reports.
© 2025 PatSnap. All rights reserved.Legal|Privacy policy|Modern Slavery Act Transparency Statement|Sitemap|About US| Contact US: help@patsnap.com