Hot-spinning cogging method based on nonuniform heating of aluminum alloy
A uniform heating, aluminum alloy technology, used in metal processing equipment, forming tools, manufacturing tools, etc., can solve the problems of excessive busbar dimensional accuracy, high temperature in the deformation zone, metal accumulation, etc., and achieve high surface hardness and good surface quality. , the effect of good metal fluidity
- Summary
- Abstract
- Description
- Claims
- Application Information
AI Technical Summary
Problems solved by technology
Method used
Image
Examples
Embodiment Construction
[0021] The present invention provides a method for hot-spinning blanking of an aluminum alloy by uneven heating. The present invention will be further described below in conjunction with the accompanying drawings and specific implementation methods.
[0022] Specific steps are as follows:
[0023] (1) The size of core mold 2 is: The length is 2500mm, and the material is die steel; the size of the aluminum alloy billet 4 is
[0024] (2) if figure 1 As shown, the mandrel 2 and the unloading ring 3 are heated to 380°C to 450°C by the heating device 1;
[0025] (3) if figure 2 As shown, the aluminum alloy blank 4 is placed on the mandrel 1;
[0026] (4) heating the upper end of the aluminum alloy billet 4 to 300°C-340°C and the lower end to 230°C-270°C through the heating device 1, and the intermediate temperature transitions naturally;
[0027] (Explanation: The temperature described in this method is the temperature of the core mold and the blank surface actually measur...
PUM
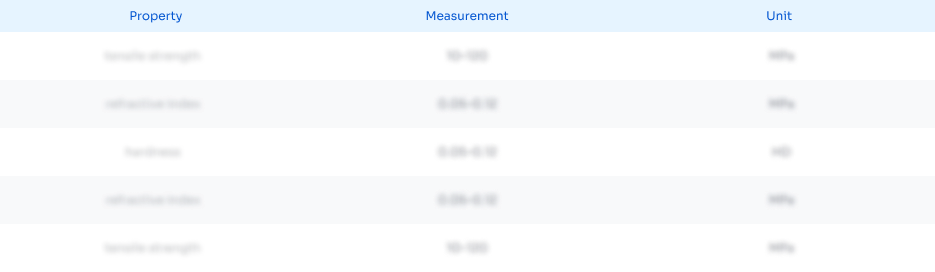
Abstract
Description
Claims
Application Information

- R&D Engineer
- R&D Manager
- IP Professional
- Industry Leading Data Capabilities
- Powerful AI technology
- Patent DNA Extraction
Browse by: Latest US Patents, China's latest patents, Technical Efficacy Thesaurus, Application Domain, Technology Topic, Popular Technical Reports.
© 2024 PatSnap. All rights reserved.Legal|Privacy policy|Modern Slavery Act Transparency Statement|Sitemap|About US| Contact US: help@patsnap.com