White-light LED chip preparation method
A technology of LED chips and white light, applied in electrical components, circuits, semiconductor devices, etc., can solve the problems of chip leakage of blue light and uneven color of white light, and achieve the effect of small luminous angle, uniform color and avoiding leakage of blue light
- Summary
- Abstract
- Description
- Claims
- Application Information
AI Technical Summary
Problems solved by technology
Method used
Image
Examples
Embodiment 1
[0015] This embodiment adopts the following steps:
[0016] The flip-chip blue LED chips 11 are arranged on the UV film 12 according to a certain spacing, the positive and negative electrodes of the flip-chip are below, and the light-emitting surface is on the front, such as Figure 1a Then, the fluorescent film 13 with the same size as the flip-chip blue LED chip 11 is bonded on the surface of the flip-chip blue LED chip 11 by a placement machine, and the adhesive between the flip-chip blue LED chip 11 and the fluorescent film 13 is silica gel 14, as Figure 1b As shown; fill the grooves between the flip-chip blue LED chips 11 with high-reflection adhesive 15 containing titanium dioxide, and bake and solidify after vacuum degassing, as shown in the following figure: Figure 1c as shown; then grind the high-reflection glue 15 to the same level as the fluorescent film 13 through the grinding machine, such as Figure 1d as shown; cut the high-reflection glue 15 along the groov...
Embodiment 2
[0018] This embodiment adopts the following steps: select a phosphor film 23 with better uniformity, stick it on the UV film 22 with high temperature resistance, and coat the phosphor film 23 with silica gel 24. The amount of transparent silica gel 24 is required to be more accurate , to avoid overflow, grab the flip-chip blue LED chip 21 with a die bonder or a sorting machine, stick the light-emitting surface of the flip-chip blue LED chip 21 on the surface of the fluorescent film 23, and bake and cure, such as Figure 2a As shown; use a glue dispenser to apply high-reflection white glue 25 in the groove between the flip-chip blue LED chips 21, and then bake and solidify after vacuum degassing, as shown in the figure. Figure 2b as shown; use a dicing machine to cut the high-reflection glue 25, silica gel 24 and fluorescent film 23 along the groove to obtain a single white LED chip, as shown in Figure 2c shown.
PUM
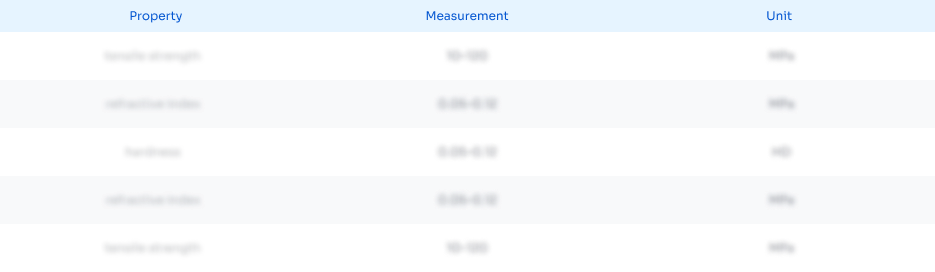
Abstract
Description
Claims
Application Information

- R&D Engineer
- R&D Manager
- IP Professional
- Industry Leading Data Capabilities
- Powerful AI technology
- Patent DNA Extraction
Browse by: Latest US Patents, China's latest patents, Technical Efficacy Thesaurus, Application Domain, Technology Topic, Popular Technical Reports.
© 2024 PatSnap. All rights reserved.Legal|Privacy policy|Modern Slavery Act Transparency Statement|Sitemap|About US| Contact US: help@patsnap.com