Stress annealing method and device capable of accurately controlling annealing process parameters
An annealing process and stress annealing technology, applied in manufacturing tools, heat treatment process control, heat treatment equipment, etc., can solve the problem of difficulty in accurately controlling annealing process parameters such as stress and temperature, inability to accurately control the annealing state of materials, and difficulty in ensuring material performance consistency. and other problems, to achieve the effect of flexible and fast temperature control, small annealing cavity, and energy saving of temperature control.
- Summary
- Abstract
- Description
- Claims
- Application Information
AI Technical Summary
Problems solved by technology
Method used
Image
Examples
Embodiment Construction
[0022] In order to make the object, technical solution and advantages of the present invention more clear, the present invention will be further described in detail below in conjunction with the examples. It should be understood that the specific embodiments described here are only used to explain the present invention, not to limit the present invention.
[0023] Attached below Figures 1 to 4 and specific embodiments to further describe the application principle of the present invention.
[0024] During the annealing process, the amorphous alloy material is automatically passed through the annealing chamber at a uniform speed, and the tensile stress, annealing temperature and transmission speed are automatically and precisely regulated online.
[0025] The present invention also takes following technical measures:
[0026] The annealing chamber is a channel-type annealing chamber 5, and the channel-type annealing chamber 5 is installed in the axial direction at the center ...
PUM
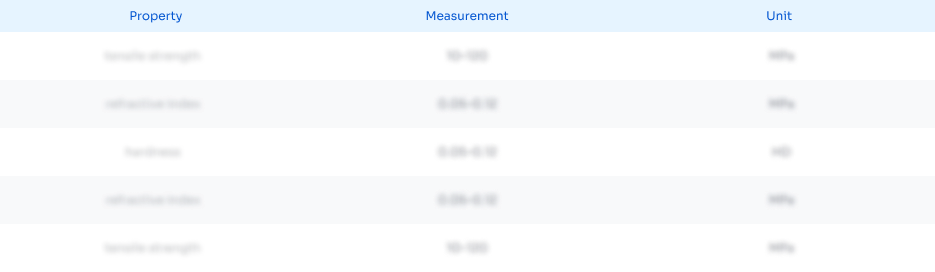
Abstract
Description
Claims
Application Information

- R&D
- Intellectual Property
- Life Sciences
- Materials
- Tech Scout
- Unparalleled Data Quality
- Higher Quality Content
- 60% Fewer Hallucinations
Browse by: Latest US Patents, China's latest patents, Technical Efficacy Thesaurus, Application Domain, Technology Topic, Popular Technical Reports.
© 2025 PatSnap. All rights reserved.Legal|Privacy policy|Modern Slavery Act Transparency Statement|Sitemap|About US| Contact US: help@patsnap.com