A method for processing waste lubricating oil
A technology of waste lubricating oil and lubricating oil, which is applied in the treatment of hydrocarbon oil, lubricating composition, hydrocarbon oil treatment products, etc., can solve the problems of poor product properties and complicated treatment process, and achieve ease of conditions, low energy consumption, and improved products color effect
- Summary
- Abstract
- Description
- Claims
- Application Information
AI Technical Summary
Problems solved by technology
Method used
Image
Examples
Embodiment 1
[0038] The present embodiment provides a method for processing waste lubricating oil, comprising the following steps:
[0039] (1) Solvent extraction: waste lubricating oil and 120# solvent oil are stirred and mixed, the mixing mass ratio of 120# solvent oil and waste lubricating oil is 2:1, the mixing temperature is 25°C, and the standing time is 3h. After standing and stratifying, The mixed oil enters the centrifugal unit;
[0040] (2) Centrifugation: The mixed oil enters the butterfly centrifuge, and the centrifuged raffinate containing polar components is thrown out. The centrifuged raffinate accounts for 4% of the mixed oil product, and 120# solvent oil in the centrifuged raffinate accounts for the centrifuged raffinate 12% of the centrifuge supernatant except centrifuge raffinate enters the membrane separation unit;
[0041] (3) The centrifugal supernatant enters the membrane module. The membrane element used is a nano-scale ceramic microfiltration membrane. The membran...
Embodiment 2
[0045] The present embodiment provides a method for processing waste lubricating oil, comprising the following steps:
[0046] (1) Solvent extraction: waste lubricating oil and 120# solvent oil are stirred and mixed, the mixing mass ratio of 120# solvent oil and waste lubricating oil is 1:1, the mixing temperature is 40°C, and the standing time is 4h. After standing and stratifying, The mixed oil enters the centrifugal unit;
[0047] (2) Centrifugation: The mixed oil enters the centrifuge, and the centrifuged raffinate containing polar components is thrown out. The centrifuged raffinate accounts for 3% of the mixed oil product, and 120# solvent oil in the centrifuged raffinate accounts for 15% of the centrifuged raffinate. %, the centrifuge liquid except the centrifuge raffinate enters the membrane separation unit;
[0048](3) The centrifugal supernatant enters the membrane module. The membrane element used is a nano-scale ceramic microfiltration membrane. The membrane separa...
Embodiment 3
[0052] The present embodiment provides a method for processing waste lubricating oil, comprising the following steps:
[0053] (1) Solvent extraction: waste lubricating oil and 120# solvent oil are stirred and mixed, the mixing mass ratio of 120# solvent oil and waste lubricating oil is 3:1, the mixing temperature is 10°C, and the standing time is 4h. After standing and stratifying, The mixed oil enters the centrifugal unit;
[0054] (2) Centrifugation: The mixed oil enters the centrifuge, and the centrifuged raffinate containing polar components is thrown out. The centrifuged raffinate accounts for 5% of the mixed oil product, and 120# solvent oil in the centrifuged raffinate accounts for 10% of the centrifuged raffinate. %, the centrifuge liquid except the centrifuge raffinate enters the membrane separation unit;
[0055] (3) The centrifugal supernatant enters the membrane module. The membrane element used is a nano-scale ceramic microfiltration membrane. The membrane separ...
PUM
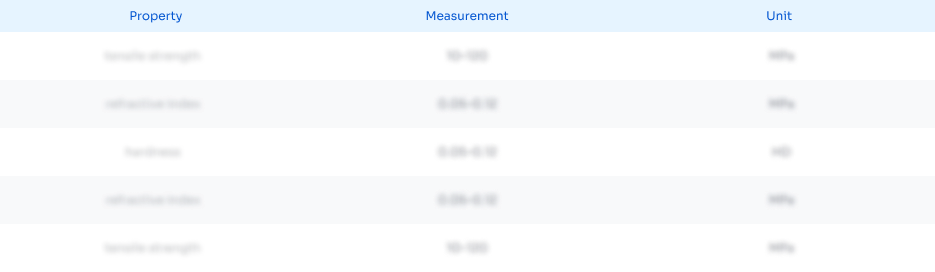
Abstract
Description
Claims
Application Information

- Generate Ideas
- Intellectual Property
- Life Sciences
- Materials
- Tech Scout
- Unparalleled Data Quality
- Higher Quality Content
- 60% Fewer Hallucinations
Browse by: Latest US Patents, China's latest patents, Technical Efficacy Thesaurus, Application Domain, Technology Topic, Popular Technical Reports.
© 2025 PatSnap. All rights reserved.Legal|Privacy policy|Modern Slavery Act Transparency Statement|Sitemap|About US| Contact US: help@patsnap.com