Method for increasing equiaxed grain rate of low-carbon high-silicon steel billet
A technology of equiaxed crystal ratio and high silicon steel, which is applied in the field of steel production
- Summary
- Abstract
- Description
- Claims
- Application Information
AI Technical Summary
Problems solved by technology
Method used
Examples
Embodiment Construction
[0020] A method for increasing the equiaxed crystal ratio of low-carbon and high-silicon steel billets. The method includes: when casting low-carbon and high-silicon steel, the composition of molten steel must satisfy 0.0011.5×10 -7 And, (Ce mass%-5.8×O mass%)>1 / 34×(Mn mass%).
[0021] The method for increasing the equiaxed crystal rate of low-carbon high-silicon steel billets further includes adjusting the superheat of the molten steel at 20-40°C, and then casting it into the copper cooling mold, passing cooling water around the cooling mold, and adopting weak Cold way.
PUM
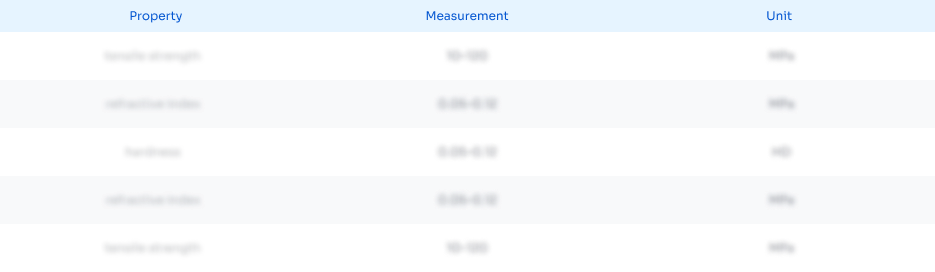
Abstract
Description
Claims
Application Information

- Generate Ideas
- Intellectual Property
- Life Sciences
- Materials
- Tech Scout
- Unparalleled Data Quality
- Higher Quality Content
- 60% Fewer Hallucinations
Browse by: Latest US Patents, China's latest patents, Technical Efficacy Thesaurus, Application Domain, Technology Topic, Popular Technical Reports.
© 2025 PatSnap. All rights reserved.Legal|Privacy policy|Modern Slavery Act Transparency Statement|Sitemap|About US| Contact US: help@patsnap.com