Shape memory alloy composite flange friction steel structure beam column splicing joint
A memory alloy and memory alloy wire technology, which is applied in building structures, buildings, etc., can solve the problems of poor performance of shape memory alloys, hinder safe application, dissipation, etc., and achieve the effect of clear force and strong practicability.
- Summary
- Abstract
- Description
- Claims
- Application Information
AI Technical Summary
Problems solved by technology
Method used
Image
Examples
Embodiment Construction
[0023] Hereinafter, the present invention will be described in detail with reference to the accompanying drawings and the embodiments.
[0024] Reference Figure 1 to Figure 4 As shown, a shape memory alloy composite flange friction steel structure beam-column splicing joint includes a column 1, a corbel 2 and a beam 3. The column 1 is connected along the beam 3 and extends out of the corbel 2, so The web of the corbel 2 and the web of the beam 3 are spliced together by a web splicing plate 5 and a web bolt 4, and the flange of the corbel 2 and the flange of the beam 3 are spliced by a flange The plate 7 and the double nut bolt 8 are spliced together, and a shape memory alloy wire 6 is wound between the double nut bolt 8 and the flange splicing plate 7, and the double nut bolt 8 applies an appropriate precondition to the shape memory alloy wire 6. stress.
[0025] There is a gap at the joint between the corbel 2 and the web and flange of the beam 3, and the bolt holes on th...
PUM
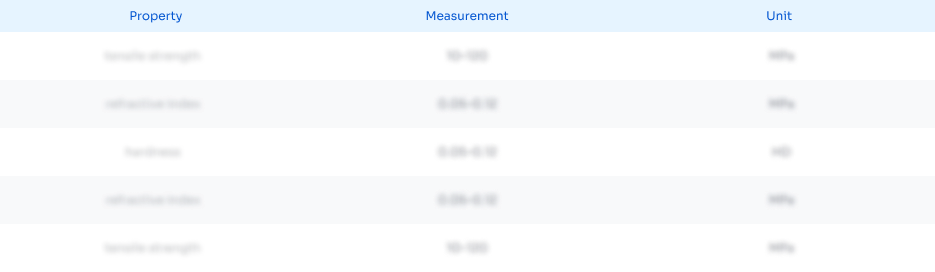
Abstract
Description
Claims
Application Information

- R&D
- Intellectual Property
- Life Sciences
- Materials
- Tech Scout
- Unparalleled Data Quality
- Higher Quality Content
- 60% Fewer Hallucinations
Browse by: Latest US Patents, China's latest patents, Technical Efficacy Thesaurus, Application Domain, Technology Topic, Popular Technical Reports.
© 2025 PatSnap. All rights reserved.Legal|Privacy policy|Modern Slavery Act Transparency Statement|Sitemap|About US| Contact US: help@patsnap.com