Welding method of rear drive axle housing assembly
A welding method and rear drive axle technology, applied in welding equipment, non-electric welding equipment, transportation and packaging, etc., can solve the problems of complex processing, poor environment, and low efficiency, and achieve improved working environment, simple operation, and low processing costs Effect
- Summary
- Abstract
- Description
- Claims
- Application Information
AI Technical Summary
Problems solved by technology
Method used
Image
Examples
Embodiment Construction
[0022] In order to make the present invention clearer, the device will be described in detail below in conjunction with the accompanying drawings. The specific embodiments described here are only used to explain the present invention, and are not intended to limit the present invention.
[0023] like figure 1 , figure 2 and image 3 As shown, a kind of welding method of rear drive axle housing assembly provided by the present invention, with respect to arc welding adopted in the prior art, this method adopts friction welding, is characterized in that comprising the following steps:
[0024] a. First process the semi-shaft sleeve 3 from the rough into a finished product, that is, firstly rough the blank 3a of the half-shaft sleeve 3, and then carry out the finish turning to process the bearing neck 3c with a stepped structure. Rough turning and finishing turning are both conventional processing methods, and then the keyway is milled on a milling machine to process the keywa...
PUM
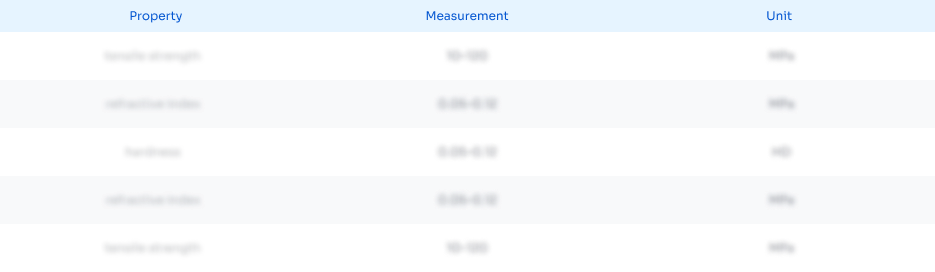
Abstract
Description
Claims
Application Information

- R&D Engineer
- R&D Manager
- IP Professional
- Industry Leading Data Capabilities
- Powerful AI technology
- Patent DNA Extraction
Browse by: Latest US Patents, China's latest patents, Technical Efficacy Thesaurus, Application Domain, Technology Topic, Popular Technical Reports.
© 2024 PatSnap. All rights reserved.Legal|Privacy policy|Modern Slavery Act Transparency Statement|Sitemap|About US| Contact US: help@patsnap.com