A kind of cement compounded with modified desulfurization ash and rice husk ash
A technology of desulfurization ash and rice husk ash, applied in the direction of cement production, etc., to achieve good dispersion, high dissolution rate, and reduce the consumption of gypsum
- Summary
- Abstract
- Description
- Claims
- Application Information
AI Technical Summary
Problems solved by technology
Method used
Image
Examples
Embodiment 1
[0029] A cement mixed with modified desulfurized ash and rice husk ash is prepared according to the weight ratio of 70 parts of cement clinker, 20 parts of rice husk ash, 5 parts of modified desulfurized ash, 2 parts of limestone and 3 parts of gypsum. Among them, the preparation method of the modified desulfurization ash is as follows: after mixing and stirring 100 parts of desulfurization ash and 100 parts of water for 30 minutes, it is naturally stored in the room for 30 days, and after preliminary crushing, it is obtained after calcining at 300 ° C for 45 minutes; The preparation method of the husk ash is as follows: first calcining the dried rice husk ash at a temperature of 350°C for 30 minutes, then calcining at a temperature of 600°C for 30 minutes, and then cooling naturally. The results of cement performance tests are shown in Table 1.
Embodiment 2
[0031] A cement mixed with modified desulfurized ash and rice husk ash is prepared according to the weight ratio of 65 parts of cement clinker, 20 parts of rice husk ash, 8 parts of modified desulfurized ash, 5 parts of limestone and 2 parts of gypsum. Among them, the preparation method of the modified desulfurization ash is as follows: 100 parts of desulfurization ash and 120 parts of water are mixed and stirred for 30 minutes, stored in the room for 20 days naturally, after preliminary crushing, and calcined at 300 ° C for 45 minutes to obtain; The preparation method of the husk ash is as follows: first calcining the dried rice husk ash at a temperature of 350°C for 30 minutes, then calcining at a temperature of 600°C for 30 minutes, and then cooling naturally. The results of cement performance tests are shown in Table 1.
Embodiment 3
[0033] A cement mixed with modified desulfurized ash and rice husk ash is prepared according to the weight ratio of 60 parts of cement clinker, 25 parts of rice husk ash, 8 parts of modified desulfurized ash, 4 parts of limestone and 3 parts of gypsum. Among them, the preparation method of the modified desulfurization ash is as follows: 100 parts of desulfurization ash and 120 parts of water are mixed and stirred for 30 minutes, stored in the room naturally for 40 days, and obtained after preliminary crushing and calcining at 300 ° C for 55 minutes; The preparation method of the husk ash is as follows: first calcining the dried rice husk ash at a temperature of 350°C for 30 minutes, then calcining at a temperature of 600°C for 30 minutes, and then cooling naturally. The results of cement performance tests are shown in Table 1.
PUM
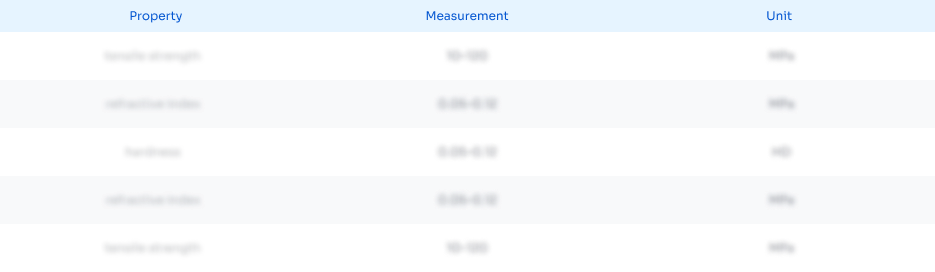
Abstract
Description
Claims
Application Information

- Generate Ideas
- Intellectual Property
- Life Sciences
- Materials
- Tech Scout
- Unparalleled Data Quality
- Higher Quality Content
- 60% Fewer Hallucinations
Browse by: Latest US Patents, China's latest patents, Technical Efficacy Thesaurus, Application Domain, Technology Topic, Popular Technical Reports.
© 2025 PatSnap. All rights reserved.Legal|Privacy policy|Modern Slavery Act Transparency Statement|Sitemap|About US| Contact US: help@patsnap.com